El Puente Hong Kong-Zhuhai-Macao

1. Introducción
El puente Hong Kong-Zhuhai-Macao (HZMB) está ubicado en el estuario del río Perla en la costa sureste de China; Se trata del cruce marítimo más largo ya construido, compuesto por islas, túneles y puentes. Une Hong Kong al este con Zhuhai-Macao al oeste con una longitud total de 55 km. El enlace se construyó de acuerdo con el estándar de autopistas de seis carriles con tres carriles en cada sentido; tiene una velocidad de diseño de 100 km/h y una vida útil de 120 años. El HZMB ha mejorado las condiciones del tráfico en los lados este y oeste de la costa del estuario del río Perla y ha fortalecido la comunicación, el transporte y la integración económica de las tres regiones, acelerando así la formación de la Gran Área de la Bahía de Guangdong Hong Kong-Macao. . Este artículo presenta el diseño y la construcción del HZMB, con un enfoque en las nuevas tecnologías involucradas en la construcción de las islas artificiales y el túnel sumergido.
2. Descripción general del proyecto
La parte principal del HZMB tiene una longitud de 29,6 km (Fig. 1); su régimen es generalmente erosionado al este y sedimentado al oeste; en el lado oeste se construyó un puente con una longitud de 22,9 km (Fig. 2(a)) mientras que en el lado este se construyó un túnel sumergido con una longitud de 6,7 km para reservar el canal de navegación principal para petroleros de 300.000 ton y permanecer dentro del límite de altura libre desde el aeropuerto de Hong Kong. Para conectar los puentes con ambos extremos del túnel, se construyeron dos islas artificiales con una superficie de 1.105 m2 cada una [1,2]. La construcción del HZMB recibió la aprobación y comenzó en enero de 2011; Se completó y entregó en febrero de 2018 y se abrió al tráfico en octubre de 2018.
En el diseño y construcción de este proyecto se realizaron varios trabajos novedosos, basados en una filosofía de ampliación e integración, estandarización, fabricación y prefabricación. El puente y su construcción destacan por las siguientes características: 1) Para la superestructura se utilizaron 400.000 toneladas de acero, batiendo así un récord mundial; 2) la capacidad anticolisión del puente se mejoró utilizando una estructura compuesta de tubos de acero en la base de pilotes; 3) los pilares del puente no-navegacional, fueron prefabricados en taller e instalados en una sola pieza para garantizar el cronograma y la seguridad y gestionar mejor el riesgo; y 4) las torres de los tres puentes navegables fueron diseñadas para simbolizar un nudo chino (Fig. 2(b)), un delfín y una vela de viento, respectivamente. En particular, la torre de los delfines se eleva a una altura de unos 100 m y pesa 2600 t; Fue prefabricado e instalado de una sola pieza. En combinación con el método de construcción moderno, este símbolo único proporciona al puente una fuerte atmósfera cultural.
Las islas artificiales y el túnel tienen las siguientes características notables: 1) La escala de trabajo fue sumamente grande; y 2) la alineación del túnel está a 20 m por debajo del lecho marino, estableciendo así un récord mundial para el túnel sumergido enterrado a mayor profundidad. Además, el lugar de trabajo se encontraba en un entorno complejo que incluía tifones, fuerte convección, inundaciones en verano y monzones en invierno; el paso de más de 4.000 buques por día; y el paso del túnel de la isla a través de la región central de conservación del delfín blanco chino, que requería un nivel muy alto de protección ambiental. En estas condiciones, la cimentación submarina, la prefabricación y la instalación marina del túnel sumergido, de más de 6 km de longitud, se realizaron sin problemas. En la siguiente discusión, presentamos las técnicas de diseño y construcción que se utilizaron para las islas artificiales y el túnel.
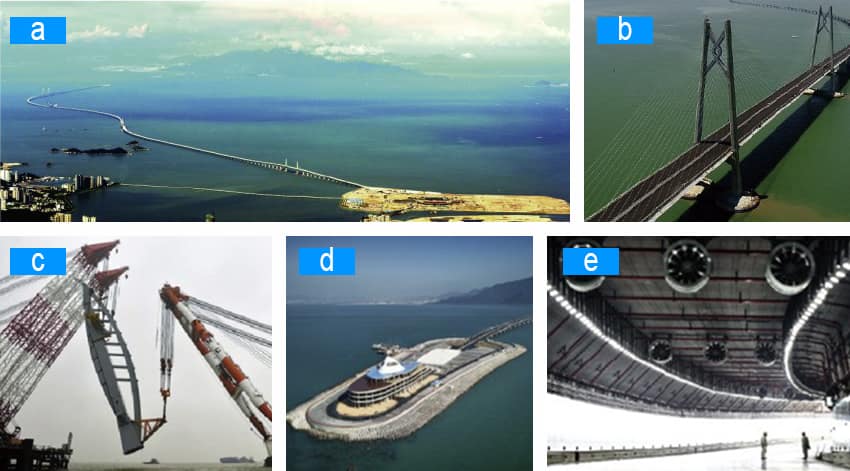
3. Técnica de construcción de islas rápida y confiable
Para crear las condiciones necesarias para la conexión del primer elemento del túnel, primero hubo que completar las islas artificiales y el falso túnel (cut and cover), que se realizó in situ en la isla. Sin embargo, el estrato de suelo blando debajo de las islas artificiales tiene más de 30 m de espesor; por lo tanto, se proyectó que la construcción de la isla tardaría tres años, lo que dejaría tiempo insuficiente para la construcción del túnel.
El suelo blando en los cimientos de las islas artificiales tenía ventajas y desventajas: en el lado negativo, llevaría a una gran cantidad de trabajo si se utilizara el método convencional de construcción de islas, es decir, si el suelo blando se mejorara mediante reemplazo total o parcial con arena o piedra. En el lado positivo, la penetrabilidad y la impermeabilidad del suelo resultaron ventajosas. Por lo tanto, se insertaron en el suelo cilindros de acero con un diámetro de 22 m, una altura de 50 m y un espesor de pared de 1,6 cm hasta una profundidad de aproximadamente 30 m. Se formó un anillo de isla insertando 60 cilindros en un patrón contiguo (Fig. 3). Se utilizaron celdas auxiliares para conectar los cilindros y se insertaron en la capa de suelo impermeable. Los cilindros y las celdas auxiliares formaron una pared impermeable que permitió el abatimiento del agua, dentro del anillo.
El método descrito anteriormente aceleró enormemente el cronograma de las siguientes maneras: 1) La construcción del muro temporal de la isla fue rápida. El gran tamaño de los cilindros de acero resultó en un menor tiempo de instalación y menos tiempo requerido para los trabajos marinos. El procedimiento que regía la línea de tiempo pasó a ser la prefabricación y transporte de los cilindros y celdas auxiliares. 2) El trabajo de cimentación fue rápido. Las paredes impermeables que formaron los cilindros permitieron el relleno de arena y la colocación de drenes verticales en la isla, para lograr una precompresión de sobrecarga con un alto índice de sobreconsolidación. Por tanto, se eliminaron una cantidad sustancial de obras de cimentación submarinas. 3) Los cilindros se utilizaron como una estructura-cerco, para la construcción del tramo de falso túnel (cut and cover), eliminando así la necesidad de excavar y sostener una zanja de 18 m de profundidad en las islas.
Al aplicar este método, acortamos el tiempo necesario para la formación de islas a siete meses. La disminución de las operaciones marinas redujo el impacto en las especies de delfines blancos chinos y en la navegación de los barcos. Cabe mencionar que el costo de construcción de la isla no superó el presupuesto, a pesar del desarrollo, investigación y ejecución de este nuevo método, porque se acortó el cronograma y se redujeron los trabajos marítimos.

4. Túnel sumergido
El túnel sumergido consta de 33 elementos de túnel y una junta de cierre. El elemento típico mide 180 m de largo, 37,95 m de ancho y 11,4 m de alto y tiene una masa de 76.000 t.
4.1. Desarrollo de instalaciones y cimientos compuestos.
El esquema de cimentación inicial requería que los pilotes de soporte comenzaran desde ambos extremos del túnel y cambiaran gradualmente a pilotes reductores de asentamientos y luego a cimientos naturales en la sección media del túnel (Fig. 4(a)). Sin embargo, en una prueba de resistencia a la carga del encepado del pilote y del lecho de grava, el asentamiento no convergió con el aumento del nivel de carga. Por lo tanto, el esquema que se implementó implicó una capa de cimentación compuesta, sobrecarga submarina y mejora del terreno (Fig. 4 (b)). La mayor parte del mejoramiento del terreno se realizó mediante pilotes de compactación de arena (SCP ground improvement). La capa de cimentación compuesta proporciona una base dura para la estructura del túnel, la sobrecarga submarina proporciona un asentamiento uniforme a lo largo del espacio y la mejora del terreno garantiza una capacidad geológica adecuada.
Para garantizar la calidad del trabajo, se desarrolló una serie de equipos especiales. Se modificó una draga de cuchara con una función de dragado plano para reducir la alteración del suelo de cimentación y aumentar la precisión a una tolerancia vertical de ±50 cm en el fondo de la zanja. Se reformó una draga del tipo «colocación de sellos» para limpiar el sedimento en el fondo de la zanja antes de colocar el lecho de grava. Se desarrolló un recipiente compactador y nivelador de piedras para colocar la capa de cantos rodados como parte de la capa de cimentación compuesta; este barco colocaba y hacía vibrar la masa de cantos rodados bajo el agua mediante dos tubos de caída y un martillo hidráulico. Además, se colocó una plataforma niveladora de grava para la colocación del lecho de grava; estaba equipado con un cabezal de succión para eliminar directamente los sedimentos locales del lecho de grava, casi sin alterar la grava colocada en su lugar.
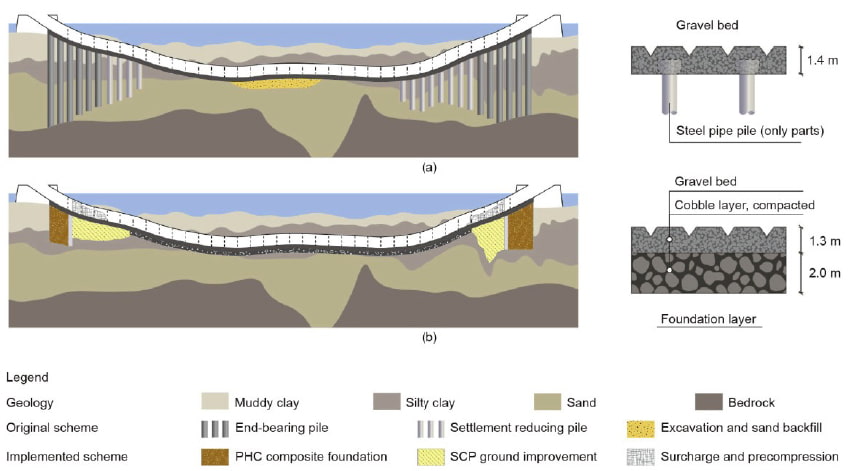
4.2. Elemento semirrígido robusto
Con el tiempo, más de 20 m de espesor de sedimento cubrirán el techo del túnel. En el futuro se volverá a dragar parte de este sedimento para actualizar la profundidad del canal de navegación. La estructura longitudinal del tipo de elemento de túnel considerado, que incluye un elemento monolítico y un elemento segmentado [3], no puede soportar una sobrecarga tan elevada de suelo sedimentario.
Se propusieron dos soluciones para reducir la carga: la primera fue el dragado de mantenimiento para eliminar el sedimento; el segundo implicó la colocación previa de material ligero sobre el túnel. Ambas soluciones requerirían un esfuerzo inmenso. Por lo tanto, se optó por no cambiar el entorno, sino cambiar la propia estructura del túnel, ya que se podría utilizar un elemento semirrígido [4] para aumentar la robustez de la estructura longitudinal del elemento. Como analogía, si se compara un elemento monolítico con una persona musculosa y un elemento segmentado con una persona flexible, entonces un elemento semirrígido tendría tanto fuerza como flexibilidad. La implementación de esta estructura redujo considerablemente las obras marítimas. El principal cambio en la estructura del elemento del túnel implicó mantener el pretensado temporal para uso permanente, en lugar de liberarlo una vez finalizada la instalación.
4.3. Rodamiento de memoria consciente
Aunque el uso de un elemento semirrígido garantizaba la seguridad de los elementos del túnel, las uniones entre los elementos serían el punto débil del túnel. El bloqueo vertical de las uniones se realizó mediante chavetas de acero postensambladas. Aunque retrasar el tiempo de bloqueo podría reducir la tensión sobre la llave de corte, más de 20 m de suelo sedimentario se cargarán gradualmente en el techo del túnel durante el período de servicio, causando una alta tensión en las llaves de corte o sus partes adyacentes. En particular, esto podría provocar grietas en el hormigón de la pared exterior, lo que provocaría problemas de corrosión. Por lo tanto, se desarrolló un soporte con memoria para proteger estas articulaciones [5]. Por ejemplo, como se muestra en la Fig. 5, el rodamiento «recuerda» la capacidad de la llave de corte en cuestión; una vez que la carga está a punto de exceder el valor memorizado, el rodamiento puede desviar la parte sobrante de la carga a los cimientos debajo del barco hundido (R1 en la Fig. 5) en lugar de a los cimientos de la estructura adyacente a través de la llave de corte. (R2 en la figura 5). De esta manera, el soporte de memoria puede liberar la estructura para que realice su máxima utilidad sin dañarse. Se pueden realizar pruebas de desgarro y fractura de materiales para fines especiales para obtener el carácter del rodamiento.
El refuerzo de la estructura suele compensar la incertidumbre geológica. Sin embargo, el tamaño de un túnel sumergido suele limitar su capacidad estructural; por lo tanto, el nivel de seguridad de la unión del elemento podría ser insuficiente. El soporte de memoria compensa este riesgo y lo traslada a uno de redundancia de la seguridad estructural.
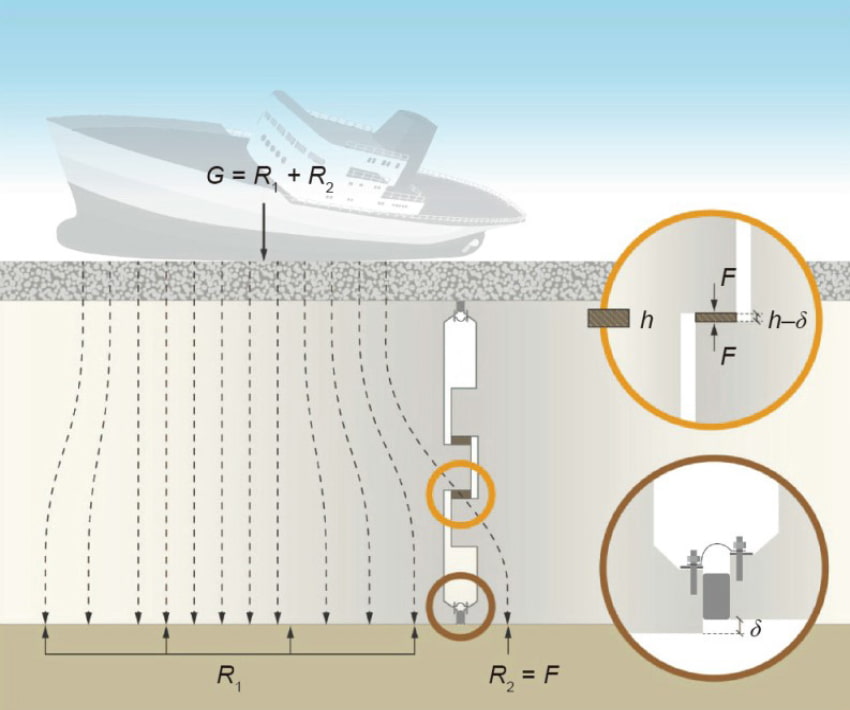
4.4. Junta de cierre desplegable
La junta de cierre se ubica entre los elementos del túnel E29 y E30, donde la cota de fondo es de 27,9 m, y donde la obra está expuesta al oleaje y corrientes. Los métodos existentes para la junta de cierre de un túnel sumergido son los métodos de ataguía, panel, bloque en V, bloque de terminales y elemento clave [6]. Todos estos métodos utilizan presión hidrostática o lechada para la conexión y la impermeabilización; en otras palabras, estos métodos son pasivos. Desarrollamos una técnica de conexión positiva e impermeabilización (water stop) para la junta de cierre [7]. La junta de cierre se construyó como elemento integral. Durante el remolque e inmersión sus dimensiones fueron menores que las de su estado final. Durante la conexión, la junta se estiró longitudinalmente hasta entrar en contacto con los elementos adyacentes. La aplicación de este método acortó el trabajo marítimo de más de seis meses a sólo tres días.
4.5. El sistema de fábrica para la producción de elementos de túneles
La elección adecuada del lugar para el patio de prefabricación de los elementos del túnel era fundamental para ahorrar tiempo y costes. Comparamos seis ubicaciones alrededor del sitio y finalmente elegimos una cantera abandonada en la isla Guishan que era la más cercana al sitio del túnel. Para producir los 33 elementos del túnel se utilizó el método de fábrica [8]. La fábrica ocupaba un terreno de 560.000 m2 y estaba dividida en zonas de producción (Fig. 6), gestión y vivienda. Participaron 1.200 personas.
Para alinearnos con el cronograma de instalación, que requería la producción de un elemento por mes dependiendo de las condiciones climáticas y marinas, producimos dos elementos cada dos meses mediante dos líneas de producción. El camino crítico en la línea de producción implicó el montaje de barras de refuerzo, encofrado y fundición de hormigón; de estos, el montaje de las barras de refuerzo era el procedimiento rector. Por lo tanto, el ensamblaje de las barras de refuerzo se discretizó aún más en tres partes en la línea de producción (el ensamblaje de la losa, las paredes y el techo) para lograr una línea suave.
La pared del túnel tiene 1,5 m de espesor. Cada segmento se fundió de una sola vez con un volumen de 3400 m3. El colado con cero grietas, de casi 1.000.000 m3 de hormigón se logró utilizando un esquema de control de agrietamiento en un entorno natural y estándar, incluido un método de colado simultáneo de sección completa.
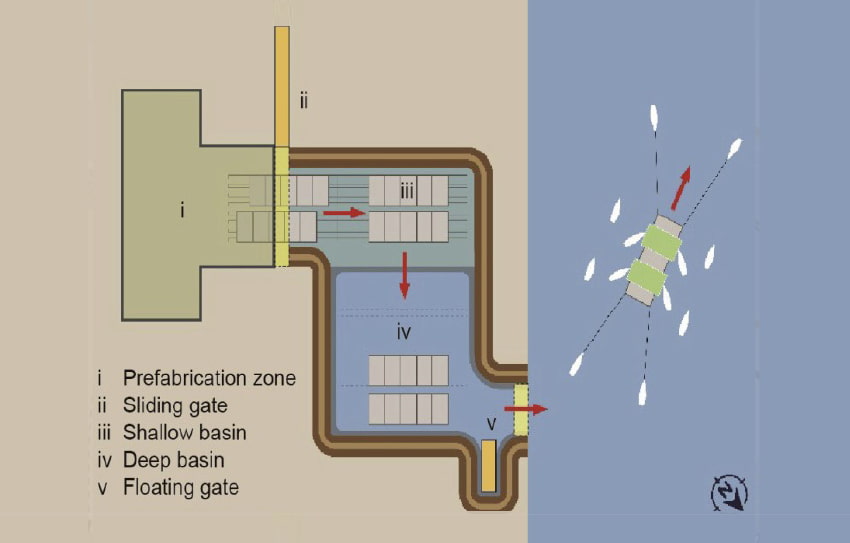
4.6. Instalación precisa de los elementos de túnel.
Los elementos del túnel fueron transportados en un canal de un ancho limitado [9]; sin embargo, si esto se saliera de control, no sólo el proyecto sufriría una pérdida significativa, sino que también el elemento varado se convertiría en un obstáculo para el intenso tráfico marítimo. Para reducir este riesgo, más de diez embarcaciones escoltaron el transporte. Para remolcar los elementos del túnel se emplearon un total de 12 remolcadores (Fig. 7). Entre ellos, cuatro remolcadores estaban conectados al elemento (dos a proa y dos a popa); los ocho remolcadores restantes navegaron al costado para controlar la posición del elemento empujando las plataformas de inmersión que se encontraban sobre el elemento cuando había una gran corriente cruzada. Para la seguridad del remolque, desarrollamos un sistema de pilotaje de navegación y monitoreamos la posición del elemento y de todos los remolcadores en tiempo real. Estos datos se mostraron en la pantalla de la sala de mando de la plataforma de inmersión, así como de todos los remolcadores. De esta forma, el capitán en jefe en la sala de mando pudo dar órdenes explícitas y en tiempo real a los demás capitanes de remolcadores. Sin embargo, fue un desafío para el capitán en jefe, que tenía una considerable experiencia en remolque en alta mar, encargar 12 remolcadores simultáneamente para mantener en rumbo un elemento de 76.000 t. Por lo tanto, antes de que ocurriera el remolque real, llevamos a cabo ejercicios de remolque de barcazas, cuatro veces.
La zanja del túnel tenía 30 m de profundidad, y esta profundidad causó dos problemas graves: 1) La velocidad de la corriente en el fondo de la zanja era a veces mayor que en la superficie del mar, lo que provocó un desplazamiento transversal inesperado de 10 cm al instalar el elemento E10; y 2) la tasa de sedimentación era rápida, de modo que incluso el sedimento de un solo día inutilizaba la instalación [10]. En dos ocasiones, mientras el elemento E15 se dirigía hacia el lugar, se observaron capas de sedimentos inesperadamente espesas a mitad del camino y el elemento tuvo que retroceder. No fue hasta la tercera vez que conseguimos instalar este elemento. La solución al primer problema fue desarrollar un sistema de previsión y alerta para la conexión; La solución al segundo problema fue desarrollar un sistema de pronóstico y alerta para la sedimentación e implementar equipos especializados de limpieza de sedimentos.
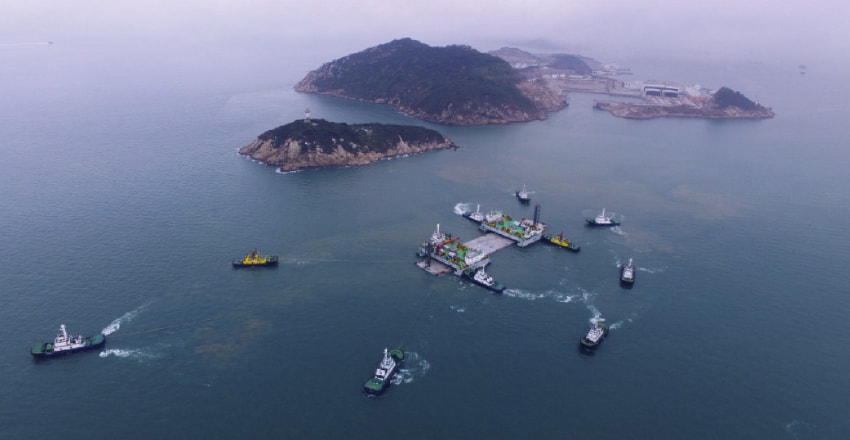
5. Comentarios finales
Después de la invasión del extremadamente severo tifón Haiyan en el Pacífico Sur en 2013, optimizamos el diseño de riesgos del proyecto y aumentamos integralmente la capacidad de prevención de riesgos del sitio. El sitio resistió las pruebas de los fuertes tifones Hato y Mangkhut.
Insistimos en una metodología de prueba y validación antes de realizar el trabajo. El contratista del túnel de la isla llevó a cabo más de 140 pruebas, incluidas pruebas del mecanismo de alojamiento de sedimentos y las capacidades de la grava, pruebas del coeficiente de fricción del hormigón y la grava y pruebas del remolque rápido [11]. Se logró cero fugas en el túnel desde la instalación de E1 en mayo de 2013 hasta el momento de escribir este documento. Un total de 33 elementos fueron sometidos a 35 instalaciones sin mayores accidentes.
Paralelamente al HZMB, se están construyendo varios puentes a gran escala en el sureste de China, como los puentes ferroviarios y de autopistas de Wufengshan y Lutongjiang en la provincia de Jiangsu, el puente ferroviario-autopista del Estrecho de Pingtan en la provincia de Fujian y el Segundo Puente Humen y enlace Shenzhong en el estuario del río Perla. En el futuro, se emprenderán más megaproyectos, incluido el cruce del estrecho de Qiongzhou hacia la provincia de Hainan, el enlace Dalian-Yantai en el estrecho de Bohai y el túnel del estrecho de Taiwán. La construcción de estos proyectos presentará problemas de ingeniería cada vez más difíciles y complejos y, por lo tanto, abrirá una nueva era de ciencia y tecnología de ingeniería de puentes y túneles en China.
Apéndice A. Material complementario
Los datos complementarios asociados con este artículo se pueden encontrar, en la versión en línea, en http://dx.doi.org/10.1016/j.eng.2018.11.002
Referencias
- Lin M, Lin W. The Hong Kong–Zhuhai–Macao Island and Tunnel Project. Engineering 2017;3:783–4.
- Lin M, Lin W, Liu X, Yin H, Lu Y, Liang H, et al. Over and under. Tunnels Tunnelling 2018:38–48.
- Saveur J, Grantz W. Structural design of immersed tunnels. Tunnelling Underground Space Technol 1997;12(2):93–109.
- Lin M, Lin W. Principles and methods for structural-type selection of immersed tunnel. China Harbour Eng 2016;36(1):1–5. Chinese.
- Lin M, Lin W, Yin H, Liu X, Liu K. Memory bearing—problem solutions of immersed tunnel immersion joint differential settlement. China Harbour Eng 2018;38:1–8. Chinese.
- Lin M, Shi F, Biao L. New technology for construction of final joints of immersed tube tunnels in Japan. China Harbor Eng 2012;4:1–4. Chinese.
- Lin M, Lin W, Wang Q, Wang X. The deployable element, a new closure joint construction method for immersed tunnel. Tunnelling Underground Space Technol 2018;80:290–300.
- Busby J, Marshall C. Design and construction of the Øresund tunnel. Civ Eng 2000;138(4):157–66.
- Lin M, Lin W, Huang W, Ning J. From mooring to mooring. In: Proceedings of the 13th ISOPE Pacific/Asia Offshore Mechanics Symposium; 2018 Oct 14–17; Jeju, Korea. Danvers: ISOPE-PAC; 2018. p. 497–501.
- Lin W, Zhang Z, Liu X, Lin M. Design for the reliability of the deepwater immersed tunnel of Hongkong–Zhuhai–Macau Bridge Project. In: Proceedings of the 27th International Ocean and Polar Engineering Conference; 2017 Jun 25–30; San Francisco, CA, USA. Int J Offshore Polar Eng; 2017. p. 1082–6.
- Lin M, Lin W, Su F, Ning J, Wang X. Immersed tunnel element towing resistance test in Hong Kong–Zhuhai–Macao Bridge Project. In: Proceedings of the 13th ISOPE Pacific–Asia Offshore Mechanics Symposium; 2018 Oct 14–17; Jeju, Korea. Danvers: ISOPE-PAC; 2018. p. 502–9.
Traducción: Ing. Jorge Coll Calderón, M.Sc., MBA