Desaladora de Carboneras, en Almería: Manantial del Mediterráneo
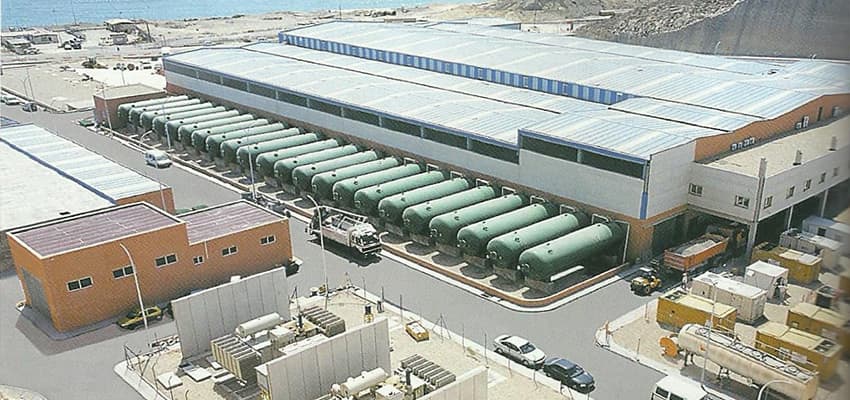
La Desaladora de Carboneras es, actualmente, la mayor planta de desalación de agua de mar de Europa. Ostenta, además, la consideración de ser la primera del mundo por su capacidad de producción, así como la primera desaladora para agua de riego de estas dimensiones (45.000 m2). Dado el abaratamiento que con éstas se logran en el proceso de desalación, así como la alta rentabilidad que puede obtenerse con la agricultura intensiva, esta planta se ha ganado el sobre nombre de ‘Manantial del Mediterráneo’.
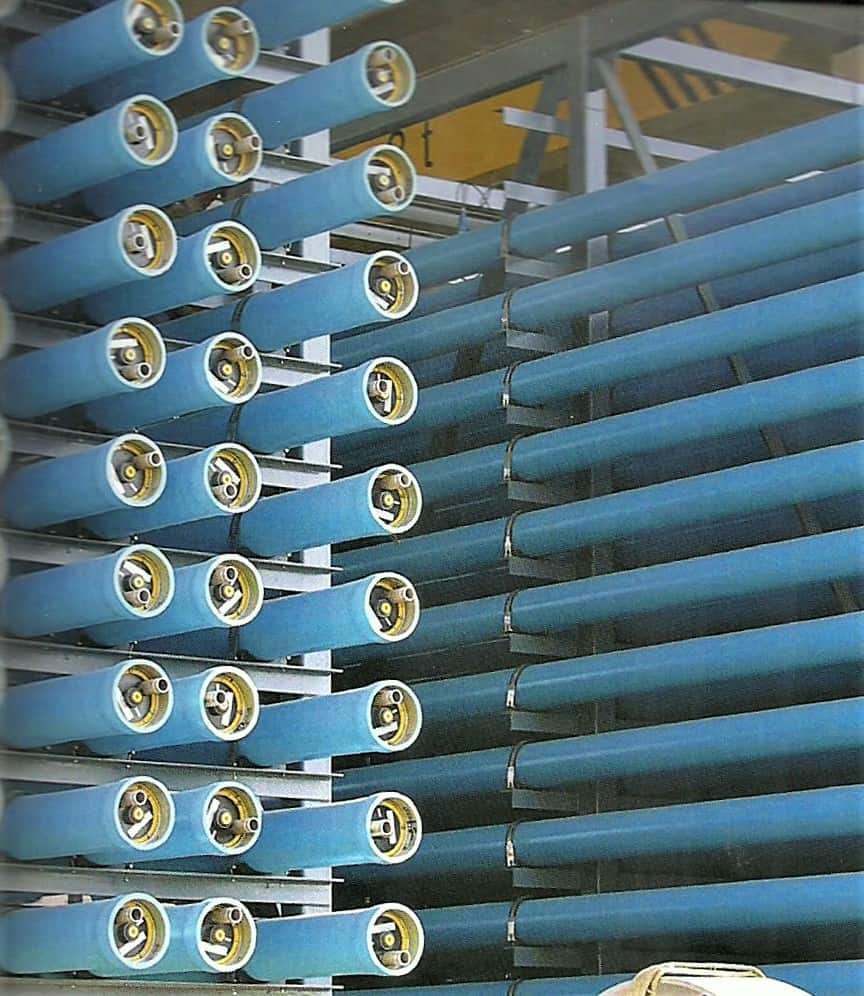
El constante avance del proceso de desertización en el sureste de la Península no tiene solución factible; pero éste no es más que el escenario en el que se desarrolla la gran inversión que constituye el Plan Global de Actuaciones Hidráulicas Prioritarias en la Provincia de Almería (en adelante PLAN ALMERÍA). Estas obras están formadas principalmente por la conexión Negratín-Almanzora (trasvase de la C.H. Guadalquivir a la C.H. Sur), la Desaladora de Agua de Mar de Carboneras (I.D.A.M. Carboneras) y la Red Principal de Depósitos y Tuberías que conducirán el agua producida hasta sus puntos de consumo.
El centro tecnológico de esta inversión es la Desaladora de Carboneras, bautizada como ‘Manantial del Mediterráneo’. Con una producción de 120.000 m3/día de agua desalada para riego en la fase actual, esta planta disminuirá el importante déficit hídrico que arrastra el levante almariense desde hace siglos. Esta carencia de agua, que cada año se ve más acusada por el crecimiento de la superficie plantada bajo plástico, provoca la continua sobreexplotación de los acuíferos y, por tanto, el intrusismo marino en los mismos.
Esta infraestructura es, en la actualidad, la mayor desaladora de agua de mar de Europa y la segunda del mundo por capacidad de producción; aunque la verdadera singularidad de esta obra recae en el hecho de ser la primera desaladora para agua de riego de estas dimensiones. Esto da una idea de hasta qué punto se ha logrado abaratar el proceso de desalación, así como la alta rentabilidad que puede obtenerse con la agricultura intensiva.
Desalación por ósmosis inversa
El agua de mar es primeramente filtrada y tratada para que en el interior de las membranas no se produzcan precipitaciones; tanto de sólidos en suspensión, como de sales. Posteriormente, se le somete al proceso central de este tipo de instalaciones que es la desalación, para la que existen varios métodos siendo el más rentable y extendido el denominado ósmosis inversa.
El fenómeno de la ósmosis natural, que tiene lugar por ejemplo en las células, consiste en que las moléculas de agua fluyen a través de una membrana semipermeable desde el medio menos salino al más salino. Como consecuencia se produce una diferencia de presión entre los dos lados de la membrana, denominada presión osmótica y que en el caso del agua de mar y del agua pura es del orden de 28 kp/cm2. En la ósmosis inversa se somete el agua salada a altas presiones para vencer el fenómeno osmótico y obtener mediante membranas semipermeables, de poliamidas aromáticas, agua con bajas concentraciones de sales. La presión óptima, para un rendimiento adecuado de la instalación, es función de la calidad del agua producto, temperatura de la misma, naturaleza de la membrana, grado de conversión, etc., en esta instalación se sitúa sobre los 67 kp/cm2.
La Planta Desaladora de Agua de Mar de Carboneras, debido a su gran capacidad de desalación, se ha dividido en dos líneas idénticas de 60.000 m3/día de agua producto cada una; a su vez, cada línea en seis bastidores de 10.000 m3/día, y finalmente cada bastidor en cuatro sub-bastidores de 2.500 m3/día. Esta estructura permite más flexibilidad de exploración y una mayor garantía de suministro, al permitir mantener la producción global de la planta durante las etapas de lavado de cada sub-bastidor.
El funcionamiento de cada línea puede realizarse de forma convencional; es decir, cada bastidor funciona de forma independiente del resto de bastidores alimentado por un equipo turbobomba, o bien como principal innovación en esta planta, en modo ‘colector común’, en esta forma de operación, el conjunto de turbobombas aspiran de un colector de agua filtrada e impulsan el agua de mar contra un colector común, desde el que se alimentan simultáneamente los seis bastidores de cada línea, de esta forma cada línea de producción funciona como un único bastidor de 60.000 m3/día de capacidad. Durante la operación de lavado de un sub-bastidor (2.500 m3/día) no se disminuye sensiblemente el caudal global de agua producto.
Para conseguir un mayor rendimiento energético, la regulación del proceso se consigue con la válvula de salida del agua producto y las válvulas de alimentación de salmuera a la turbina, evitándose la pérdida de carga, y por tanto de energía, que se produce en la válvula situada en la impulsión de la turbobomba que permanece abierta al 100% durante la operación.
Por último, hay que destacar que, aunque la tecnología empleada es convencional, no lo es tanto el tamaño de la instalación, lo que ha hecho necesario el diseño específico de algunos equipos, principalmente los grupos turbobomba de 949 m3/h a 700 m.c.a. y las válvulas de macho Ø = 500 mm.
Durante el proceso de desalación del agua de mar se suceden varias etapas físico-químicas, encaminadas a proteger y prolongar la vida útil de las membranas, que se describirán a continuación y de forma breve, así como las obras civiles que los albergan, siguiendo un orden lógico para una más fácil comprensión y lectura.
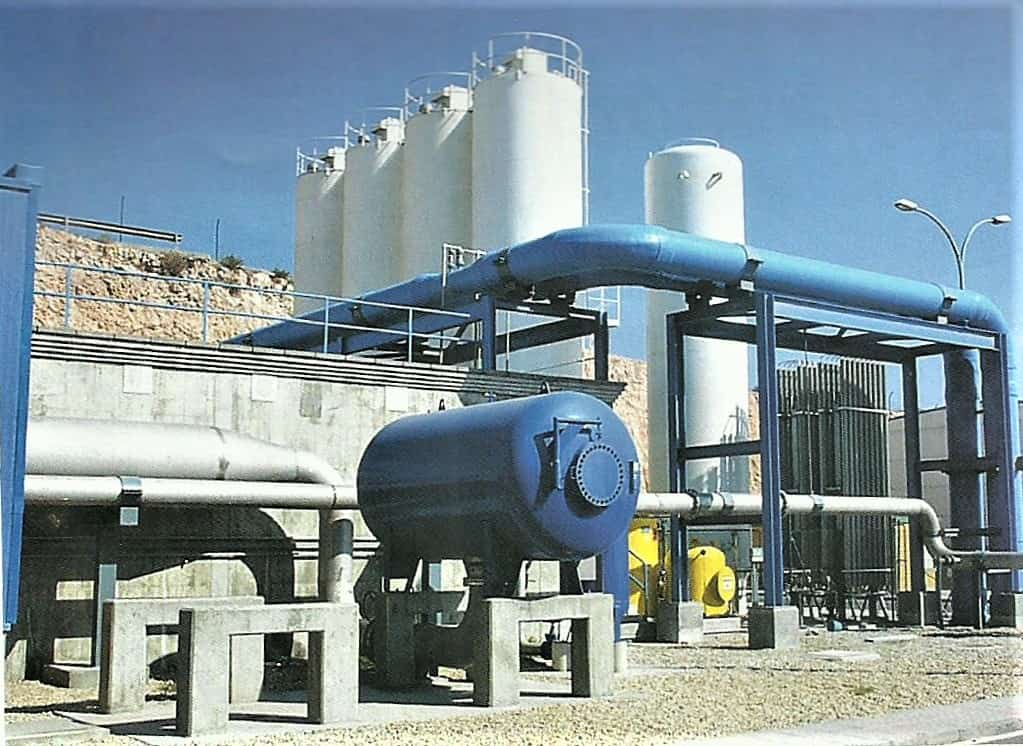
De visita por la planta
Toma de agua de mar abierta
La toma de agua bruta se efectúa mediante la denominada toma de agua de mar abierta, compuesta por dos tuberías de poliéster reforzado con fibra de vidrio (PRFV) y Ø = 2000 mm. Estas tuberías se adentran unos 150 m en el mar y desde el punto de toma a la cota -18 m hasta la entrada en la instalación, concretamente en los canales desarenadores a la cota -4 m, todo su recorrido se realiza bajo la cota del nivel del mar, por vasos comunicantes, con lo que se evitan bombeos, sifones, etc.
Tras la captación, el agua llega a través de las tuberías hasta la zona donde se producirá el desarenado de la misma y donde comienza el tratamiento del agua bruta. Aquí se adiciona hipoclorito sódico como biocida y oxidante, además está prevista la posibilidad de adición de algún reactivo auxiliar (permanganato como oxidante fuerte).
Desarenador
Es una obra subterránea, situado a la cota -4,00 y de 85,5 m de longitud por 16 m de ancho, con una altura de 11 m, perimetralmente se cierra con muros de 70 cm de espesor, fuertemente armados y posee una losa superior, a base de placa alveolar prefabricada, apta para tráfico de vehículos y sustentada por pilares jácenas prefabricadas. Desde su solera y hasta la cota +1.20 m, se ha dividido en seis canales, dotados en sus extremos de compuertas murales logrando el cierre de cada canal para las labores de mantenimiento y una rejilla de desbaste a la entrada. Estos equipos están construidos en acero inoxidable AISI 904-L.
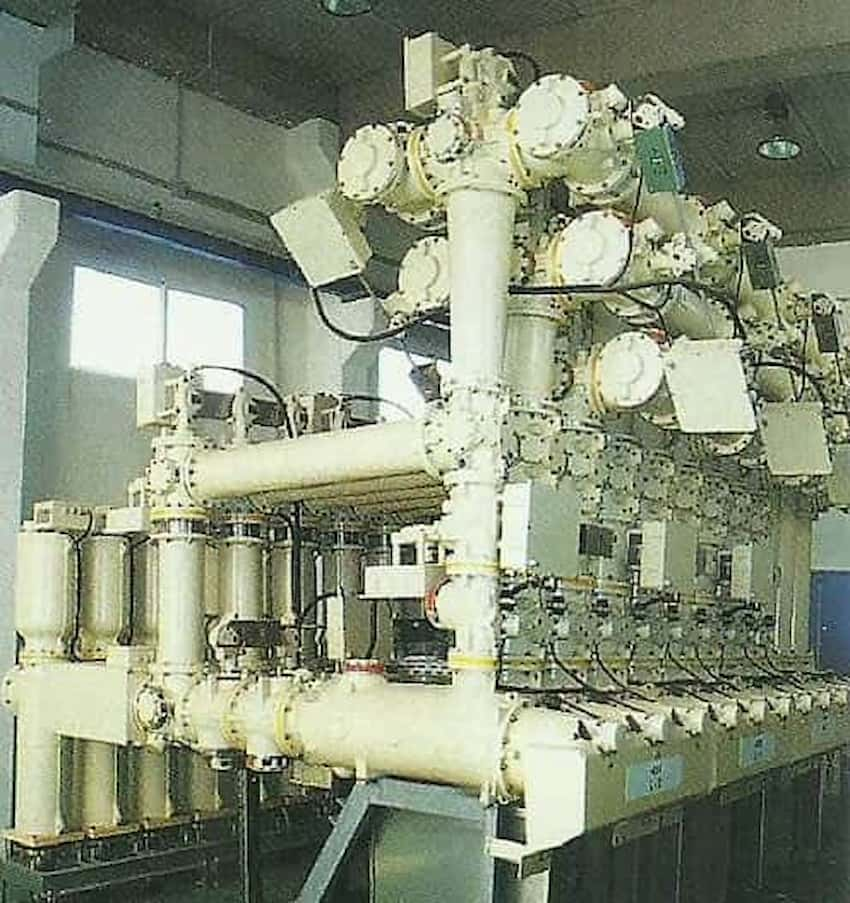
Cántara de aspiración de agua de mar
Se sitúa al final de los canales desarenadores y cuenta con un volumen entorno a los 3.000 m3, siendo estructuralmente similar al anterior.
Debido al tipo de terreno y a la cercanía a la costa, el nivel freático está situado a la cota del nivel del mar; por ello, durante la construcción de estos edificios, fue necesario el bombeo continuado, hasta finalizar el recinto y conseguir un lastre mínimo que compensara la flotabilidad de la estructura. Por otro lado, el tipo de terreno encontrado, calcarenita, favoreció de forma importante el proceso constructivo respecto a las arenas que se esperaban bajo el nivel freático, lo que permitió la excavación sin necesidad de utilizar tablestacas ni otro tipo de entibación.
Todo el hormigón armado utilizado en la planta, tanto en zonas húmedas como inundables (soleras, canaletas, apoyos, etc.), se ha exigido como clase de exposición general la IIIc y específica +Qc debido a las frecuentes inundaciones que pueden sufrir por agua osmotizada y agua de mar, ambas altamente agresivas.
Edificio de bombeo
Es, también subterráneo y de estructura similar a los anteriores, se sitúa a la cota +1.20 m y está destinado a albergar los equipos encargados de impulsar el agua de mar captada, hacia la nave de proceso. Tanto este edificio de como la cántara de aspiración anexa están dimensionados para albergar los equipos de una posible ampliación de la planta.
Desde este punto, la planta se divide en dos líneas independientes de producción, cada una cuenta con 6+1 bombas centrífugas de eje vertical de 220 kW alimentadas a 6 kV, construidas en a AISI 904 y para 930 m3/h y 6 bares de presión asistidas por un sistema de vacío para conseguir el cebado de las mismas, junto a la línea de bombas hay una sala eléctrica donde se sitúan las cabinas de control de motores (CCM’s) y dos trafos para servicios auxiliares de 400 kVA.
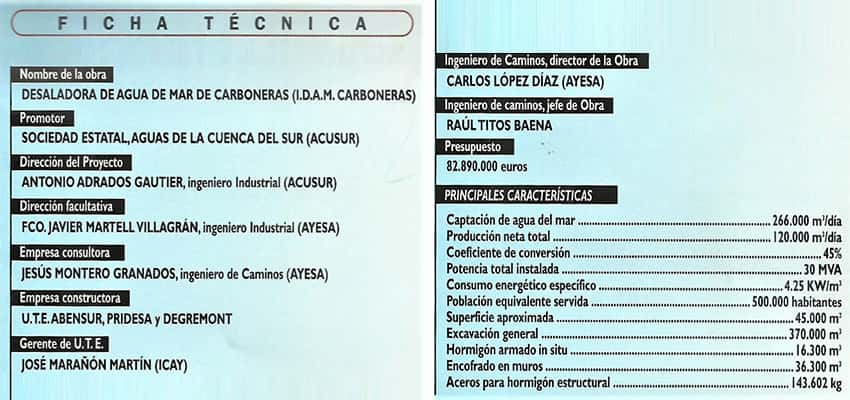
De este edificio parte una tubería PRFV de Ø = 1000 mm por cada línea, que conduce el agua bruta hasta los filtros de arena que funcionan en paralelo, en estas líneas se puede proceder a la dosificación de un coagulante, así como de ácido sulfúrico para ajustar el pH óptimo y mejorar la filtración. Estos tienen forma cilíndrica de L = 11,6 m y Ø = 3.2 m y disponiéndose 22 ud por línea, ocupando ambos laterales de la nave de proceso de forma que el frente de filtros con toda la valvulería, queda dentro de la misma. Los filtros están compuestos por dos granulometrías de arena diferentes de tallas efectivas 2 y 0,9 mm, alcanzándose una velocidad de filtración máxima de 7m/h con dos filtros en lavado. El lavado se realiza con agua de rechazo, salmuera, por contracorriente con 1+1 bomba centrífuga por línea de 550 m3/h y 2 bares y 1+1 soplantes de 1850 Nm3/h a 1,5 bares.
Bajo las líneas de filtros, se sitúan sendas balsas para la neutralización del agua de lavado de membranas previa al vertido al mar junto con el agua de salmuera.
Nave de ósmosis inversa
Después de esta filtración, el agua bruta entra en la nave de ósmosis inversa, verdadero corazón de la instalación, en el que tiene lugar el proceso de desalación del agua del mar. Está constituida por un edificio de planta rectangular de 101.20 x 72 m de planta y una altura máxima sobre rasante de 13,50 m. estructuralmente la nave es de tipo porticada con 5 vanos cuyas luces son 15, 8.5, 25, 8.5 y 15 m. estos pórticos están formados por pilares y vigas prefabricados en hormigón armado, de varias dimensiones y tipologías.
La cimentación está formada por 6 muros de hormigón armado de 3 m de altura y 0,60 m de espesor, que se apoyan sobre zapatas corridas de 1,90 m de anchura. A la cota de +10,60 se dispone la solera de 40 cm de canto sobre la que apoyan todos los equipos de la nave, a excepción de las turbobombas que lo están sobre bancadas independientes con objeto de no transmitir las vibraciones propias de su funcionamiento al resto de la edificación.
Junto a las turbobombas se han dispuesto dos galerías subterráneas visitables de 2,00 x 2,10 m, por las que se abastece eléctricamente a todos los equipos presentes en la nave y en el edificio desarenador y bombeo de agua de mar.
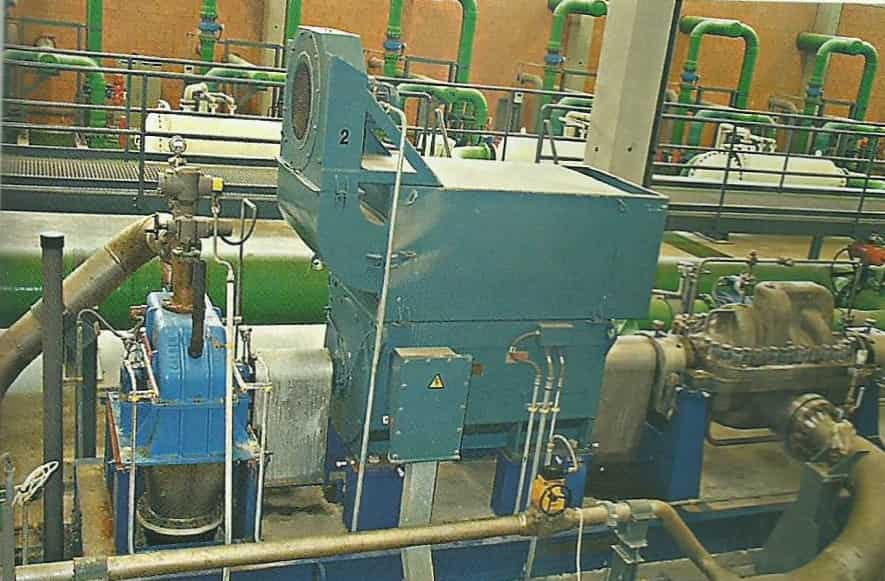
El cerramiento de la nave se realiza con un zócalo de bloque visto rugoso sobre el que se apoyan paneles alveolares pretensados con acabado de chino lavado. Sobre éste se sitúa una franja de iluminación natural continua, realizada con U-Glass de 1.20 m de altura. La cubierta está formada por correas de hormigón pretensado sobre las que se disponen placas tipo sándwich de 30 mm de espesor, con acabado de PLASTISOL 100 micras en la exterior y PVDF 60 micras en la cara interior, que deberá soportar un ambiente más agresivo.
Filtros de cartucho
El primer proceso físico que tiene lugar en el interior de la nave es una microfiltración en los seis filtros de cartucho que, dispuestos en cada línea, tienen un poder de corte de 20 micras absolutas. Inmediatamente después se adiciona dispersante al agua filtrada para evitar la precipitación de coloides no filtrados que provocarían incrustaciones en las membranas, y bisulfito sódico, como agente reductor para eliminar el exceso de oxidantes que también dañaría las membranas.
Las membranas de ósmosis inversa se fabrican enrolladas en espiral alrededor de un tubo que recoge el agua osmotizada o de permeado, y su forma consiste en un cilindro de 1.2 m de longitud y 20 cm de diámetro. Éstas se colocan en número de siete dentro de los tubos o cajas de presión, que se disponen ordenadamente hasta 144 unidades por bastidor. El número total de membranas de la planta es de 12.096, perfectamente identificadas y posicionadas unívocamente en la planta, para lo que previamente han sido ensayadas unitariamente en fábrica anotando sus parámetros de producción. Una vez en funcionamiento, existe la posibilidad de analizar el agua producida por cada caja de presión.
La presión necesaria para que el proceso de ósmosis tenga lugar se consigue mediante 6+1 turbobombas por línea, que constan de un motor eléctrico de 1.500 kW alimentado a 6 kV, una bomba capaz de impulsar 949 m3/h de agua de mar, a 70 bares de presión y una turbina Pelton, acoplada al mismo eje a la que se conduce el agua de salmuera, aún con presiones de hasta 60 bares, que permite recuperar en torno a 850 kW de forma que se reduce notablemente su consumo eléctrico por m3 de agua producido.
Edificio de oficinas y control
Está adosado a la nave de proceso, tienen tres plantas así como un sótano que está destinado a albergar las diferentes conducciones eléctricas. En la planta baja se han instalado los cuadros de control de motores de los equipos, dos transformadores para servicios auxiliares de 2.050 KVA y dos más de aislamiento. En la planta primera están situadas las oficinas, los servicios y los vestuarios de los operarios, así como el laboratorio. En la zona central, se sitúa una amplia ala de control con buena visibilidad sobre la planta y en el lateral de la nave de proceso se instala un corredor panorámico que recorre transversalmente la instalación.
Desde los bastidores de O.I. el agua permeada se conduce a la zona donde se realizará la remineralización. Para albergar estas instalaciones de postramiento del agua producto se ha previsto una zona anexa al depósito, en la que se disponen los sitios de cal y las instalaciones necesarias para el afino del agua producida.
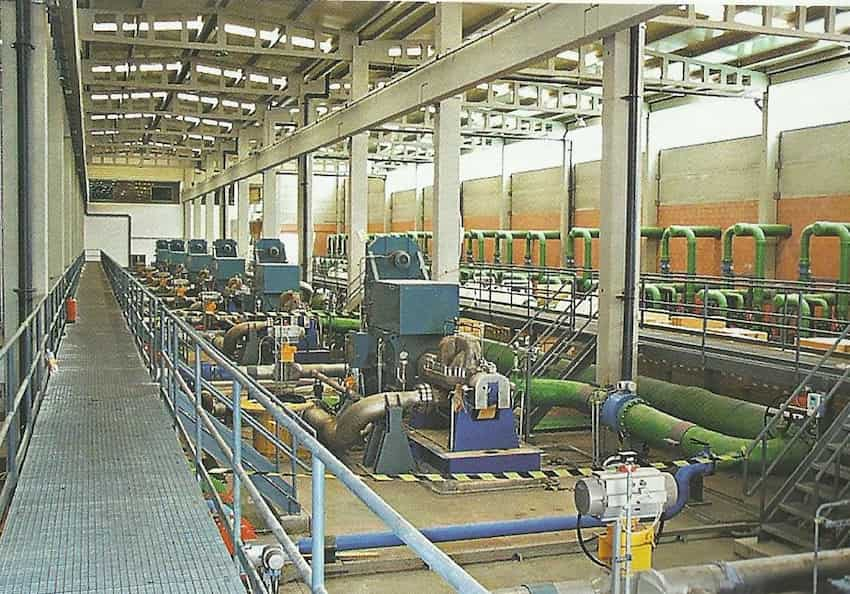
Con posterioridad se vierte al depósito de regulación e impulsión que tiene una capacidad de 1.500 m3. Se trata de un recinto rectangular delimitado por muros de H.A. y estructura prefabricada similar al resto de edificios.
Edificio de bombeo de agua producto
Se encuentra adosado al depósito, en él que se instalan las 8 bombas de impulsión de agua producto 830 m3/h y 60 m.c.a. ejecutadas en fundición de acero inoxidable 316. Desde aquí parte la tubería de impulsión, de fundición centrifugado de f 1000 mm, con una longitud de aproximadamente 1.200 ml hasta llegar a la balsa de acumulación de 97.000 m3.
La tubería de vertido de los rechazos del proceso de la planta desaladora se ha diseñado en PRFV de Ø 1600 mm discurriendo por gravedad, desde la planta hasta el punto de vertido situado a unos 1.300 ml. En este punto, la salmuera se vierte al canal de descarga de agua de refrigeración de la central térmica anexa, unos 200 ml antes de su llegada al mar para mejorar su dilución, de esta forma se produce una mezcla previa (entorno 20/1) que diluye el vertido de salmuera disminuyendo los posibles efectos negativos en el ambiente marino, concretamente en la Pradera de Poseidóneas presente en la Isla de San Andrés situada a apenas 3 km. El vertido de salmuera también mejora el impacto del vertido de la central térmica al disminuir ligeramente la temperatura del mismo.
Por último, la alimentación eléctrica se efectúa desde la central térmica vecina mediante dos líneas subterráneas de 132 kV, cada una con potencia suficiente para 70 MVA, que se reciben en una subestación blindada interior desde la que se alimenta un trafo de 30 MVA, disponiéndose otro en reserva no instalado.
Publicación original: 2003