Viaductos del AVE Madrid-Barcelona. Subtramo IV-A, en Montblanc (Tarragona): Singularidad Técnica
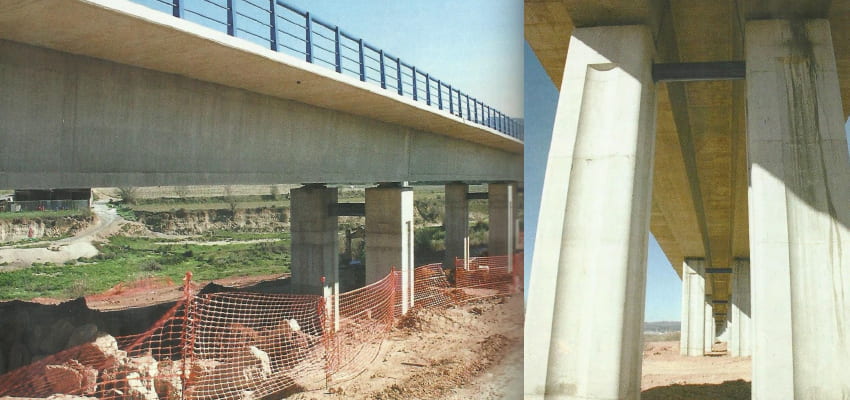
Más de ocho kilómetros de plataforma y un trazado en planta que dibuja una curva cercana a los 7 mil metros de radio, caracterizan el subtramo IV-a del AVE Madrid-Barcelona. En él destaca la singularidad de ejecución de sus viaductos y pasos superiores.
Originalidad y trascendencia que se ha centrado tanto en las técnicas de construcción como en los materiales empleados en el desarrollo de estas infraestructuras.
Dentro del conjunto de obras de la línea de alta velocidad Madrid-Barcelona se encuentra el tramo Lleida-Martorell. A éste pertenece el Subtramo IV-a, que se localiza geográaficamente dentro del término municipal de Montblanc, en Tarragona.
Esta obra tiene una longitud total de 8.040 m, con un trazado en planta que prácticamente en su totalidad, dibuja una curva de 6.800 m de radio. El perfil longitudinal es variable, con pendientes máximas del 2,50%.
En función de su tipología, esta obra puede dividirse en 6 zonas: Un primer tramo de 5.500 m en desmonte y terraplén, con sus correspondientes obras de paso y drenaje transversal; un paso superior, para el ramal de salida de la autopista A-2 hacia Montblanc; uno superior para la carretera C-14 (Reus-Tárrega); un segundo tramo que comprende un viaducto de 652 m sobre el río Anguera; un tercer tramo de 936 m de terraplén entre viaductos; así como, un viaducto final de 952 m sobre la llanura de inundación del río Anguera.
Del conjunto de estas obras destacan, por su trascendencia y originalidad, la ejecución de los viaductos y los pasos superiores, ya que el resto, dominado por el movimiento de tierras, carece de singularidad.
Viaductos
Entre los dos viaductos suman una longitud de más de un kilómetro y medio. El primero, que se ubica sobre el río Anguera, está compuesto de 16 vanos isostáticos de 34 m y un tramo central hiperestático de 108 m, que está compuesto de tres vanos continuos de 36 m de luz. El segundo viaducto dispone de 28 vanos isostáticos, también de 34 m.
Es decir, que entre ambos viaductos disponen de 44 vanos isostáticos que se resuelven con 88 vigas tipo cajón de 2,45 m de altura, 2,30 m de ancho en la base y 2,79 m en la parte superior. A esto hay que añadir, como luego se señala, seis unidades de 36 m para los tres vanos hiperestáticos, lo que hace un total de 94 unidades de vigas.
Dado el plazo de ejecución de la obra, tan importante en los tramos del AVE, y ante la inseguridad del suministro por parte de las empresas de prefabricación; así como, por las dimensiones y el peso unitario de las vigas (200 toneladas) que suponían una complicada logística de transporte por carretera, se optó por la instalación de una planta de prefabricación a pie de obra, con lo cual se podían controlar diariamente los plazos parciales y el final de la obra, con total garantía en cuanto al suministro y transporte de las vigas.
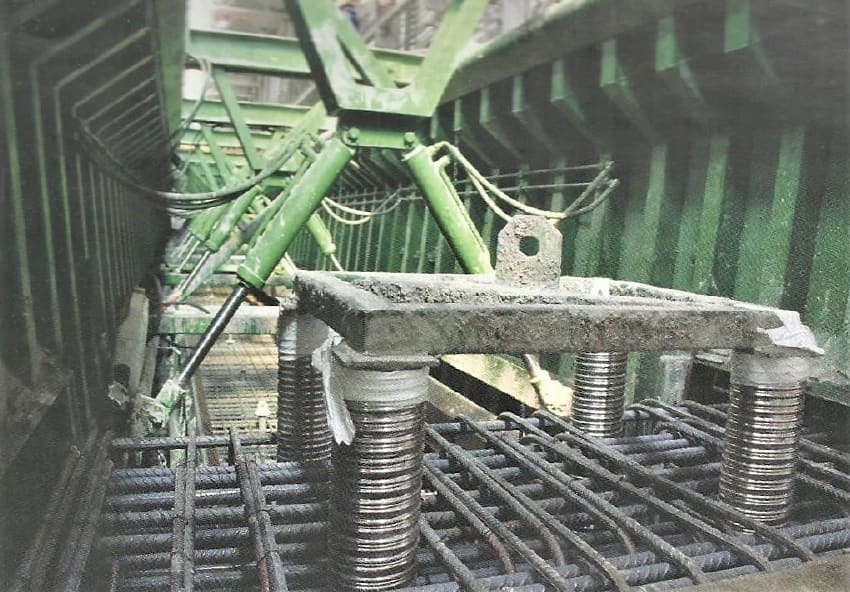
El citado edificio de fabricación consistía en una superficie cubierta de planta rectangular de 1.500 m2, a salvo de las inclemencias del tiempo y con la iluminación necesaria para poder trabajar en horarios nocturnos. En su interior se ubicaban dos bancadas paralelas de 36 y 38 m de longitud con un puente grúa en el interior de la nave para la manipulación de armaduras y encofrados.
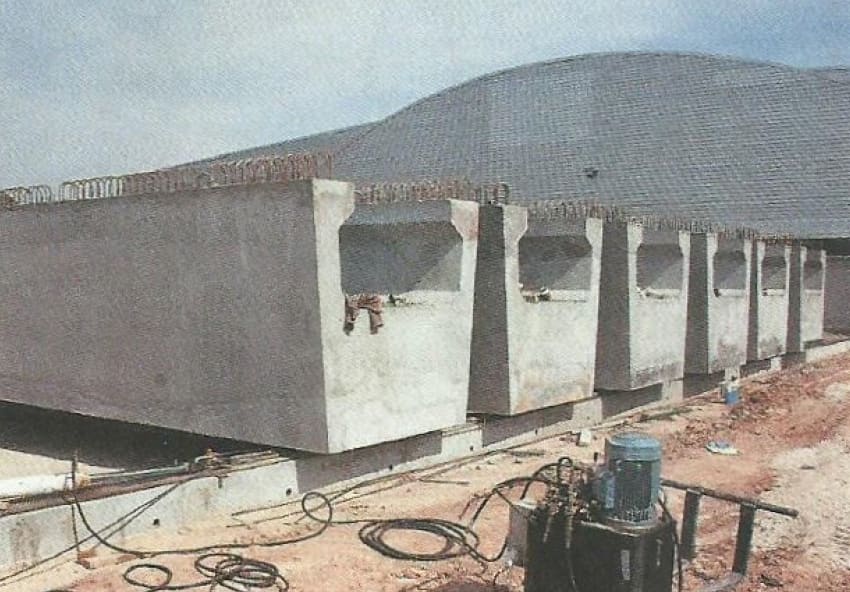
A nivel del suelo, y como encofrado de la parte inferior de la viga, cada bancada disponía de su propio encofrado metálico, plano y fijo en la solera de la nave. Para el encofrado de alzados, tanto interior como exterior, existía un juego de encofrados metálicos que se trasladaba de una bancada a otra mediante el puente grúa.
Con el fin de reducir los tiempos de desencofrado y manipulación de la viga hasta el lugar de acopio, era imprescindible reducir al mínimo los medios mecánicos. En este caso, la zona de acopio de vigas estaba situada a ambos lados de la planta de prefabricados. Cada zona de acopio, consistía en dos muretes longitudinales de hormigón armado, separados entre sí unos 30 m. Estos, de 40 cm de anchura estaban coronados por una chapa plana de acero inoxidable, sobre la cual se deslizan desde las bancadas hasta el acopio exterior.
Para ello, en los dos extremos del encofrado metálico de fondo, a un metro de distancia de los bordes de cada bancada, se empotraban por debajo de la solera los dos muretes del acopio, perpendicularmente al eje de la viga, de forma que tras el hormigonado y el curado, la viga prefabricada queda apoyada sobre dos almohadillas de neopreno+acero+teflón que se han posicionado sobre los carriles citados. Cada una de las almohadillas soporta un peso de 100 toneladas. La parte inferior de las dos almohadillas (teflón) se apoyan sobre la chapa de acero inoxidable de los carriles-murete (rozamiento teflón-acero mínimo). Tras el desencofrado de la viga, ya se puede ‘tirar’ con dos gatos hidráulicos (uno por cada carril) desde el exterior de la planta de prefabricados y deslizar la viga por los carriles hasta el acopio (esfuerzo de tiro de tan solo 5 toneladas por gato).
Las almohadilles permiten, además, absorber el giro en los apoyos de la viga cuando se cortan los cables de pretensado.
El encofrado exterior de la viga cajón fue metálico, llevando incorporados los pasillos con barandillas para realizar las tareas de hormigonado y control. El encofrado interior se compone de módulos divididos en dos partes, que se unen mediante gatos hidráulicos para facilitar la labor de encofrado y desencofrado. Por otra parte, el encofrado interior incorpora también unas vigas de cuelgue que sirven de tirante en el arriostramiento en cabeza de dos encofrados (interior y exterior).
Después de unas 30 horas de que la viga fuera hormigonada, y siempre que las resistencias del hormigón superaran los 40 kp/cm2, se procedía al corte de los cables de pretensado, transmitiéndose la compresión al hormigón de la viga mediante estos cables. En este momento, gracias a la compresión de la zona inferior de la viga, se produce una contraflecha que despega la viga del encofrado plano inferior, y pasa a quedarse apoyada en las almohadillas de teflón.
Cada zona de acopio, a ambos lados de la planta de prefabricación, tenía una longitud de 45 m, lo que permitía acopiar unas 14 vigas en cada lado, es decir, unas 30 en total. En el acopio, éstas permanecen biapoyadas sobre los dos muretes-carril. Una vez que el acopio está lleno, se procedía a la carga en vehículos de transporte especial y a su traslado hasta la obra, donde eran izadas y colocadas en su ubicación definitiva.
En cuanto a la capacidad de producción, se consiguió fabricar cuatro vigas semanales, y puesto que cada uno de los vanos del viaducto consta de dos vigas, se concluye que se puede prefabricar semanalmente vigas para unos 70 m de viaducto, en condiciones de plena producción.
Durante el proceso de fabricación de vigas, se ha seguido un exhaustivo control de todos los materiales y medios de producción, tales como dosificaciones y resistencias del hormigón, controles de la ejecución y controles del tesado.
Técnicas especiales
Los apoyos tradicionales de neopreno zunchado, frente a las solicitaciones de compresión, cortante y momento flector, están limitadas por la magnitud de las deformaciones tangenciales que se producen en el neopreno, y que pueden llegar a alcanzar valores elevados en los bordes libres, lo que podría conducir a su rotura por agotamiento del material a esfuerzo cortante.
Los aparatos de apoyo tipo POT consisten en una almohadilla de elastómero protegida por una carcasa de acero, que sella perfectamente el componente elastomérico, permitiéndole actuar como un fluido viscoso incomprensible bajo la acción de cargas verticales y ofreciendo una resistencia mínima a la rotación alrededor de cualquier eje horizontal.
Entre la placa superior de la carcasa de acero y el elastómero se intercala un espejo de acero inoxidable pulimentado y una lámina de teflón protegida con un lubricante especial (grasa de silicona) que evita su abrasión. El teflón presenta excelentes propiedades frente al envejecimiento y a la humedad, con un buen comportamiento a la fatiga, un alto poder antiadherente y un bajo coeficiente de rozamiento.
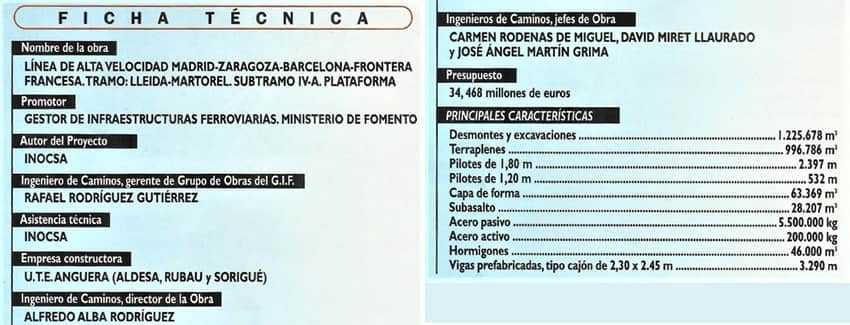
Tanto la placa superior como la inferior incorporan pernos de anclaje en acero zincado. En la coronación de las pilas se dejan los alojamientos para los pernos inferiores del apoyo. Una vez presentado y nivelado el apoyo POT, se encofra perimetralmente y se rellena con mortero de alta resistencia, quedando así instalado el apoyo en la pila. Posteriormente se ubica la viga prefabricada, haciendo coincidir los pernos superiores del apoyo colocado en la pila con los alojamientos practicados en las vigas prefabricadas. Una vez colocada la viga sobre el apoyo, se rellenan con mortero los huecos entre los pernos superiores y los alojamientos en la viga.
Otra novedad importante en la ejecución de los viaductos de esta obra ha sido la forma de ejecutar los tableros. Con el fin de conseguir una sección totalmente colaborante, se suprimieron las chapas o placas de encofrado perdido, ya que disminuyen la sección útil. Para evitar el empleo de jabalcones y con el fin de eliminar los hormigonados parciales en voladizos, se optó por el empleo de una autocimbra, diseñada para hormigonar completamente el tablero, en toda su anchura definitiva para cada uno de los vanos.
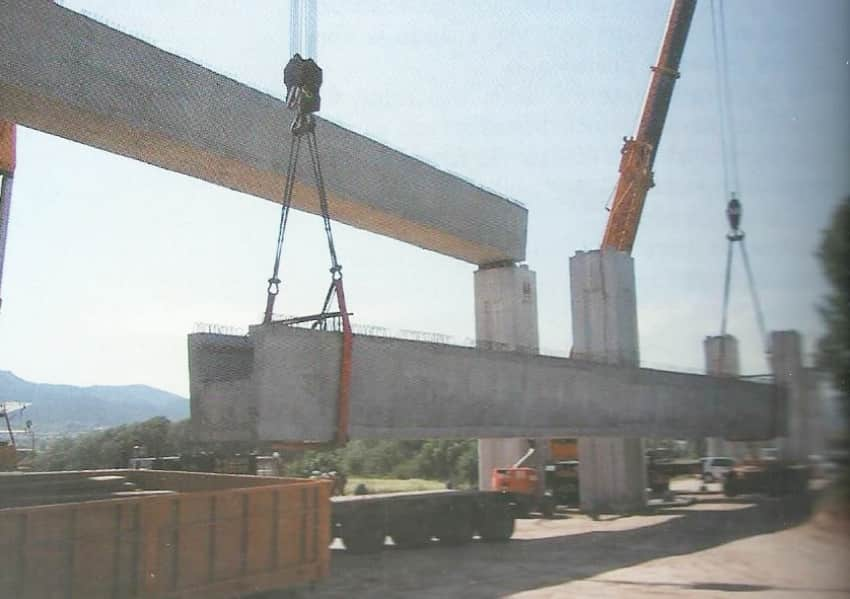
La autocimbra consistía en diez tramos de celosía metálica, de entre 3,20 y 3,80 m de anchura, en el sentido longitudinal del viaducto, por lo que colocados uno junto a otro se cubren los 35 m de luz de cada vano. Se diseñaron y construyeron para que pudieran colgarse de las vigas prefabricadas para lo cual se dejaron unos orificios pasantes en el alma de la viga cajín, coincidiendo con el eje longitudinal de la viga. Los citados orificios sirven para introducir un perno roscado que se coincidir con la zona de cuelgue de cada tramo de la autocimbra, una vez izado con grúa y posicionado el tramo de autocimbra, se pasa el perno roscado por el orificio de la viga y mediante las oportunas pletinas y tuercas queda suspendida la autocimbra de las vigas prefabricadas.
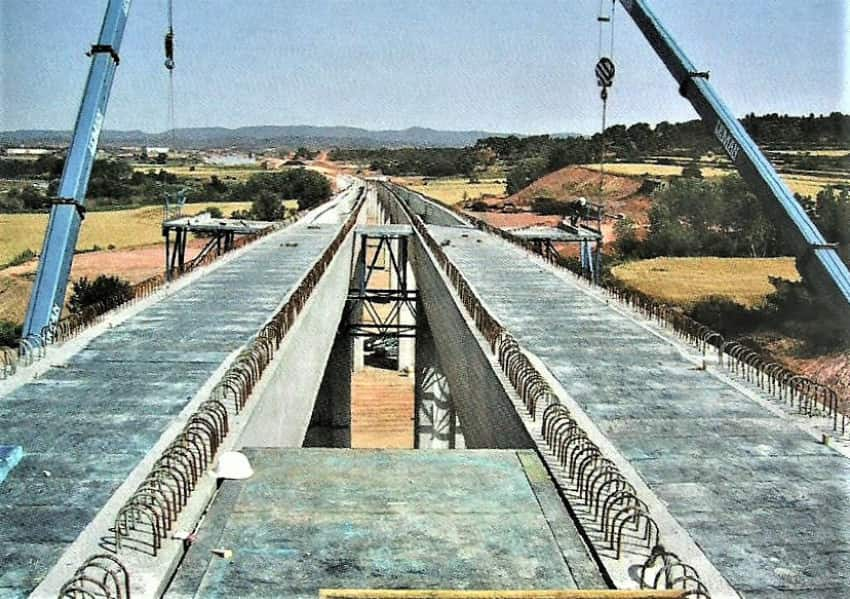
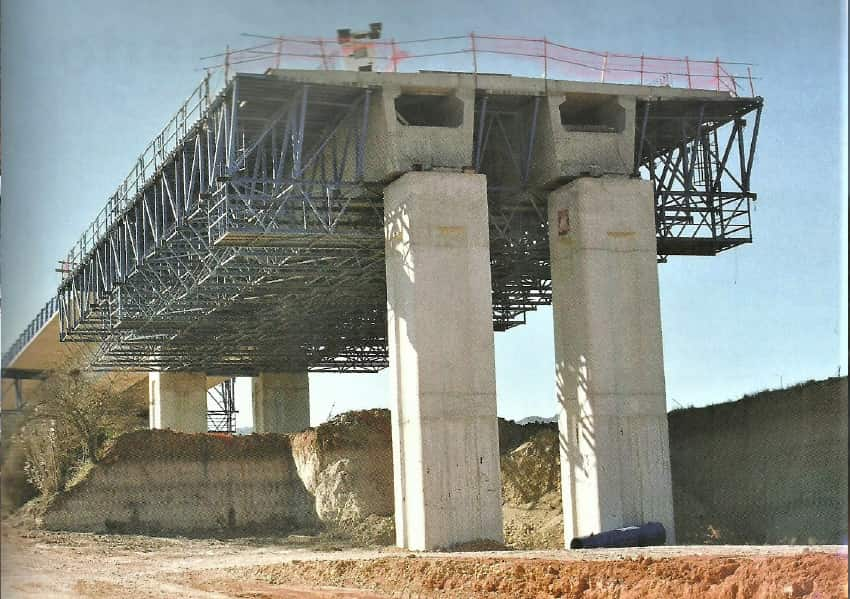
Cada tramo de autocimbra tiene 16 m de anchura, en el sentido transversal al eje del viaducto, lo que permite cubrir los 14 m de anchura de tablero y dejar un metro de pasillo en cada uno de los dos voladizos para la ubicación de barandillas provisionales.
El proceso de desencofrado de un vano y encofrado del siguiente es rápido. Esta operación se completa en unas 10 horas de trabajo para lo cual son necesarias dos grúas (que efectúa tanto las laboras de encofrado como de desencofrado) y unos seis oficiales encofradores. Durante la jornada siguiente se ferralla el tablero por la mañana y se hormigona durante la tarde. Cuando las resistencias del hormigón superar los 150 kp/cm2 (un día de curado) se repite la operación de desencofrado del vano hormigonado y encofrado paralelo del vano siguiente. Con este ciclo, se han venido hormigonando dos tableros por semana (35 m de longitud por 14 m de anchura cada uno).
Tramo hiperestático
El viaducto sobre el río Anguera incluye un tramo continuo (hiperestático) de 108 m de longitud (vanos de 33+42+33 m), comprendido entre las pilas 5, 6, 7 y 8, que coincide con el paso sobre el cauce principal del río Anguera.
Este tramo se resuelve mediante tres parejas de vigas de 35.967 m, que van unidas entre sí mediante 10 barras postensadas a 27,6 Tn. Primero se colocan las 2 vigas extremas del tramo (parejas 1 y 3) y a continuación la central (pareja N.º 2), al tiempo que se van colocando las barreas de postensado entre ellas.
El tablero tiene las mismas características geométricas y de armado que en los tramos isostáticos a excepción de las familias de cables de tesado de tablero. Estos cables se dividen en tres familias; las dos primeras (20+20 cables de 9 torones de 0,6”) poseen un anclaje pasivo y otro activo (es decir, sólo se tensa desde el anclaje activo porque el pasivo queda hormigonado con el tablero), cuya finalidad es la de ejercen una comprensión en la sección sobre pilas para reducir los momentos negativos que se producen en ese apoyo. La tercera familia (8 cables de 9 torones de 0,6”) tiene la función de unión final entre las fases previas de hormigonado, a la vez que colabora con las familias 1 y 2.
Por otra parte, todo el tramo va unido a la pila 8 mediante un macizo de anclaje adherido inferiormente a las vigas, de forma que esta pila actúa también como estribo fijo.
La ejecución del tramo hiperestático se realiza en ocho fases:
- Colocación de las vigas extremas del tramo (pareja de vigas 1 y 3).
- Colocación de las vigas centrales (pareja de vigas 2).
- Tesado de las barras de unión entre vigas.
- Hormigonado de los tramos de momentos negativos (los que se encuentran sobre apoyos intermedios; pilas 6 y 7 en una longitud de 90 m cada lado de la pila).
- Tesado de cables de familias 1 y 2.
- Hormigonado de los tramos extremos y centrales.
- Tesado de cables de la familia 3.
- Unión y tesado de barras de atado entre el tramo hiperestático y la pila 8.
Enlace con la A-2
La intersección entre la línea del AVE y el ramal de incorporación a la autopista A-2 desde Montblanc se ha resuelto mediante una estructura que posibilita su ejecución a pesar de los servicios afectados de gas y oleoducto, consistente en una losa postensada única para los cuatro carriles de circulación.
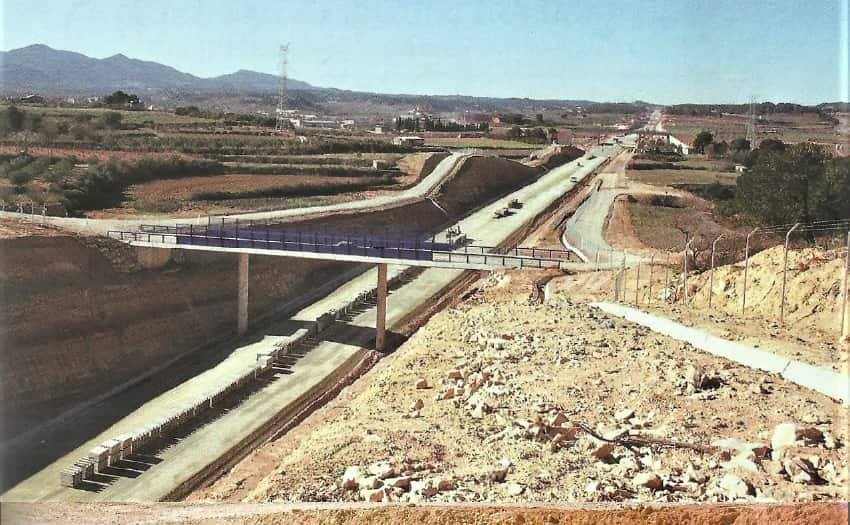
Las dimensiones del tablero resultante, en el sentido del ramal de autopista, oscilan entre 28 y 26,5 m de anchura variable, 50 m de longitud y un canto de 75 cm.
El paso final consta de tres vanos, de los que el central entre pilas tiene un gálibo horizontal de 23,14 m (para el paso del ferrocarril) y dos vanos laterales de unos 13,30 m de distancia entre pila y estribo.
Se ejecutaron cinco pilotes de 1,2 m de diámetro para la cimentación de los dos estribos y otros siete con sus correspondientes pilas para cada uno de los dos apoyos intermedios.
La losa del tablero se ejecutó mediante cimbra cuajada, correas metálicas y encofrado fenólico. Se dispusieron 36 tendones para el postensado, en el sentido longitudinal de la losa. Tras el hormigonado y curado del hormigón de la losa, se realizó un primer tesado hasta una tensión unitaria de 84,6 kp/mm2, lo que equivale a una fuerza de tezado de 225 toneladas por cada tendón. Una vez alcanzada en el hormigón la resistencia de 400 kp/cm2, se realizó el tesado definitivo con una fuerza de 379 toneladas por tendón, comprobándose que los alargamientos unitarios fuesen de 349 mm. Finalmente, se inyectaron las vainas con mortero de cemento.
Intersección con la C-14
El paso bajo la carretera comarcal C-14 se resuelve mediante una bóveda prefabricada triarticulada, apoyada sobre muros de hormigón armado ejecutados ‘in situ’, con lo cual se consigue respetar el gálibo horizontalmente de 15 m y aumentar el gálibo vertical hasta un total de 9,28 m, desde la cabeza del carril hasta la clave de la bóveda.
La longitud total de la bóveda resultante es de 42,5 m con muros de apoyo de 5 m de altura y piezas prefabricadas prácticamente circulares de radio de 7,5 m. junto a cada muro de sustentación de las piezas prefabricadas, por la parte exterior, se ha construido un nicho longitudinal de 2,0 x 1,8 m libres interiores, con el fin de dar continuidad a través de ellos a las cuentas de drenaje longitudinal de la plataforma. La cimentación de los muros de apoyo de la bóveda es de tipo directo mediante zapatas independientes de hormigón armado.