Barrera dinámica y sostenimiento de talud en el Ferrocarril Curitiba – Paranaguá
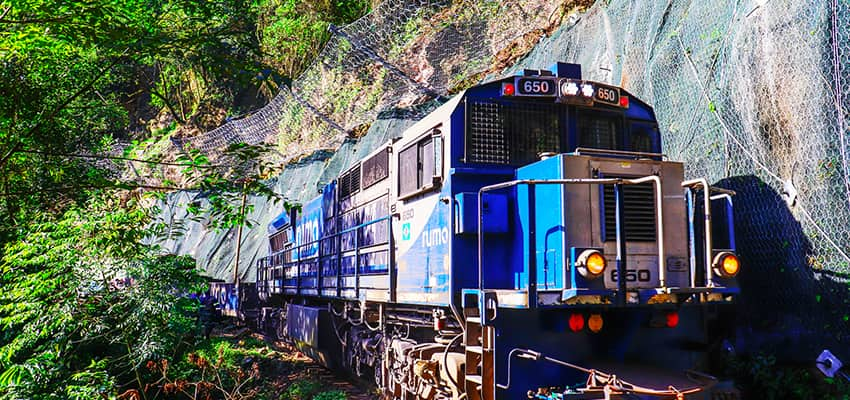
Ubicado en el Estado de Paraná, el Ferrocarril Curitiba – Paranaguá es una importante ruta que conecta el puerto de Paranaguá con la capital del estado, Curitiba. La construcción del ferrocarril comenzó en 1880 y el entonces emperador de Brasil, Pedro II, colocó la primera piedra de la construcción el 5 de junio de ese mismo año. Las obras duraron cinco años y sólo contó con mano de obra asalariada, principalmente inmigrantes italianos, polacos y alemanes. En 1894, un año antes de la inauguración completa de la vía férrea, se inauguró el puente São João, que es el puente más largo de toda la vía férrea, con 112 m de largo y 55 m de altura, ubicado cerca del sitio de construcción. La princesa Isabel, junto con la comitiva real realizó el viaje completo partiendo de Paranaguá con destino a Curitiba el 16 de noviembre del mismo año.
Desde su apertura hasta la actualidad, este ferrocarril representa una de las rutas más importantes para el transporte de mercancías desde el interior del estado de Paraná hasta el puerto. Actualmente, el ferrocarril es operado por Rumo Logística, que transporta varios tipos de carga. También hay un tren turístico de pasajeros que hace este recorrido.
La vía cuenta con 14 túneles, 10 estaciones intermedias, así como 30 puentes y viaductos a lo largo de sus 110 km de longitud, de los que gran parte se encuentra en medio de la accidentada orografía de la Serra do Mar y en medio de uno de los más amenazados biomas en territorio brasileño: la Mata Atlántica. Todo este contexto histórico, geológico y ambiental influyó en la elección de la solución adoptada.
Debido a la irregularidad del relieve, además de los perfiles y técnicas de excavación realizadas en el momento de la construcción, es común tener problemas de inestabilidad superficial en algunos tramos de la vía férrea, principalmente en el tramo de montaña entre la ciudad de Morretes y Curitiba. En 2020 se presentó caída de bloques de roca sobre las vías del tren en el km 62, cerca a la ciudad de Morretes, lo que puso en riesgo la seguridad y continuidad de las operaciones.
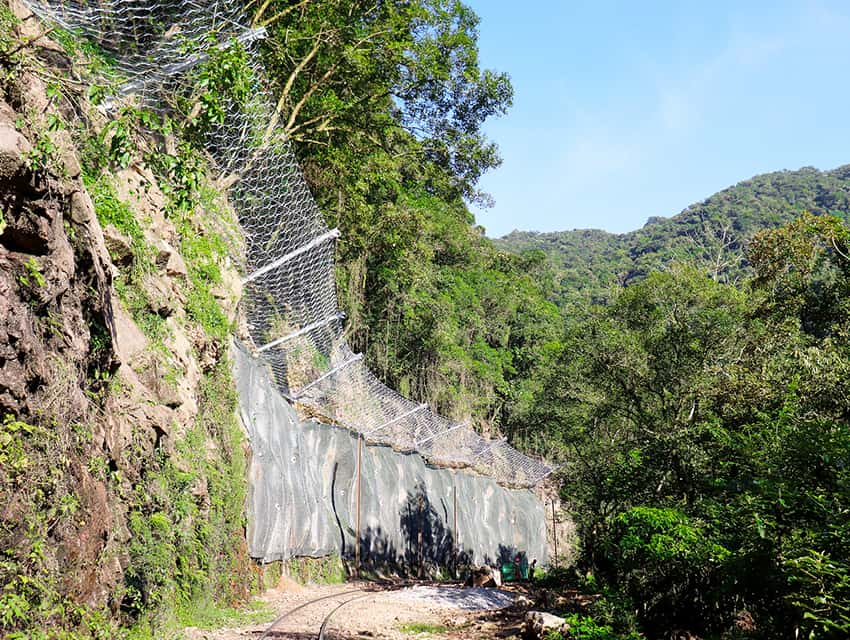
En vista al riesgo existente en este tramo, ubicado cerca del puente São João y a unos 3 km de la estación Marumbi, la empresa Rumo Logística buscó alternativas para proteger la línea férrea consultando con Maccaferri quienes, luego de un minucioso análisis de las condiciones locales de la obra, sugirieron algunas opciones de intervención.
En las visitas de campo se notó la presencia de bloques con potencial de caída a lo largo de todo el talud desde muy cerca de los rieles extendiéndose hasta la parte alta del talud, ya compuesto por terreno natural y con presencia de vegetación densa. Por cuestiones ambientales y económicas, se descartó un sistema de sostenimiento con mallas en toda la superficie inestable del talud ya que para tal aplicación habría que deforestar una gran área de la Mata Atlántica. La mejor alternativa para este desafío fue una solución que, con el menor impacto posible en el sitio, pueda garantizar que los bloques de roca que se desprendan de la parte superior del talud no lleguen a la vía férrea. En base a estos supuestos, Rumo Logística, en conjunto con Maccaferri, optó por proteger el área del km. 62 de la vía férrea con el uso de una barrera dinámica contra desprendimientos de rocas.
Esta solución se utilizó por primera vez a mediados de la década de 1970 en Europa. Su concepto es la instalación de una estructura interceptora, que se fija al suelo mediante anclajes perforados y puede interceptar las trayectorias de los bloques que caen, impidiendo que lleguen al área de interés a proteger. Esta solución se fue desarrollando a lo largo de los años siguientes contando en 2008 con su primer estándar de ensayo y producción (ETAG 027), hoy denominado EAD 340059-00-0106. Hoy en día esta solución ha sido aplicada en cientos de ocasiones en todo el mundo.
Una gran ventaja de las barreras dinámicas, que la convirtió en la mejor solución para el kilómetro 62 de la vía férrea, es su bajo nivel de intervención en la geometría y condiciones del terreno local, sin necesidad de despejar grandes superficies ni realizar mayor movimiento de tierra para su instalación. Esto supone una ventaja no sólo desde el punto de vista ambiental, sino también desde el punto de vista operativo dada la dificultad de acceso a la zona de intervención y el hecho de que las obras tendrían que realizarse con la vía férrea en funcionamiento, interfiriendo lo menos posible con el tráfico de los trenes.
Con base en las dimensiones de los bloques inestables y la topografía local, fue posible estimar las posibles trayectorias de estos bloques utilizando el software comercial para análisis probabilístico Rockfall, desarrollado por Rocscience. De este análisis de trayectoria se pudo extraer las posibles alturas de impacto, utilizadas para determinar la altura de la barrera dinámica, y las posibles velocidades de impacto, determinando así la energía de impacto que la estructura de intercepción tendría que disipar.
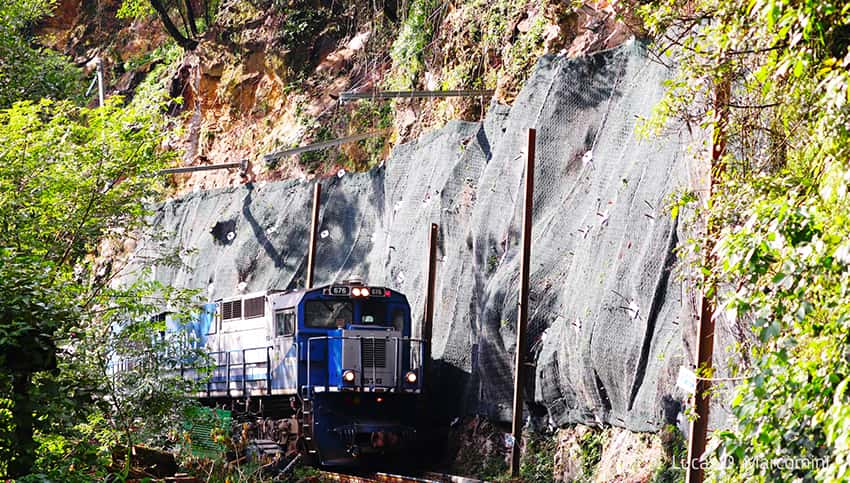
Luego de estos análisis se determinó que la barrera más adecuada para garantizar la seguridad de las operaciones en el km 62 sería el modelo de barrera dinámica certificada con 2000kJ de capacidad de absorción de energía y 4m de altura. De acuerdo con las condiciones topográficas locales y la posición de los bloques inestables, la longitud de la barrera se definió en 80 m. Además, debido a la deformación del orden de 5 m que tendría la malla de la barrera en el momento del impacto, la barrera debía colocarse a una distancia segura del derecho de vía, lo que configuraría una ubicación de la estructura a una altura de 10 m con respecto a la vía.
Las barreras dinámicas están compuestas por un kit de elementos que llegan a la obra con todos los componentes optimizados para que la instalación sea lo más sencilla posible en obra. Incluso con las precauciones tomadas por parte de Maccaferri, para enviar la barrera en estas condiciones, hubo numerosos desafíos y lecciones aprendidas en la etapa de instalación. La primera y sin duda la más limitante de todas fue la necesidad de realizar la construcción con el ferrocarril en operación prácticamente todo el tiempo, con interrupciones ocasionales. Esta restricción imposibilitó el uso de maquinaria pesada como grúas o plataformas elevadoras (manlift); sin embargo, esto no limitó la instalación de las estructuras. Otro desafío fue realizar todos los accesos al área de intervención y el izado de los materiales mediante el uso de cables y eslingas, lo que sin duda impactó el tiempo de ejecución de la obra, pero había sido prácticamente imposible de ejecutar con otro tipo de sistema diferente a las barreras dinámicas. Se debe destacar, que cualquier trabajo que se realice en los márgenes de las vías férreas, especialmente en tramos de montaña, requiere un gran esfuerzo de coordinación en la logística de gestión de equipos y materiales, incluso más que en otro tipo de trabajos.
La barrera dinámica se instaló para contener bloques de roca provenientes de la parte alta del talud, sin embargo, aún quedaba una franja de 10m sin protección contra desprendimiento de material que se extendía desde el inicio de la barrera dinámica hasta el pie del talud, cerca de los rieles. Para este tramo se adoptó la solución de revestimiento cortical que consiste en instalar una malla metálica reforzada en la cara del talud, la cual se fija mediante anclajes pasivos que aferran la porción de roca inestable, presente en la superficie del talud, al macizo rocoso intacto. En este caso, se utilizó la malla MacMat® HS de Maccaferri y una configuración de pernos, espaciados cada 2m, tanto en horizontal como en vertical.
El uso de los dos sistemas en conjunto – barrera dinámica y revestimiento superficial con MacMat® HS – garantizó la seguridad de las operaciones en el km 62 de esta ruta, tan importante para la economía del estado de Paraná, estabilizando el macizo rocoso en su parte baja y conteniendo los eventuales bloques que pudieran caer desde la parte alta del talud. Maccaferri estuvo presente in situ en varias etapas del proyecto, desde su concepción, a finales del 2020, hasta la entrega de la obra en mayo del 2021.