Puente Juscelino Kubitschek, en Brasilia: Un monumento funcional
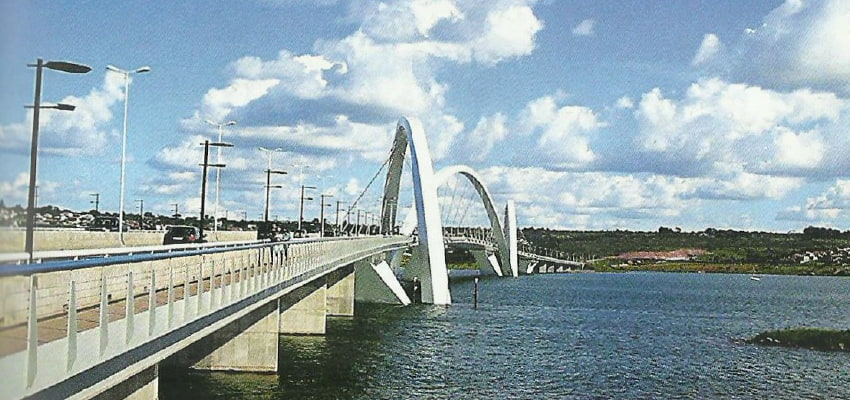
Brasilia, ciudad considerada por la UNESCO Patrimonio Cultural de la Humanidad, ha enriquecido su ‘monumentalidad‘ al incluir dentro de su recorrido turístico al nuevo puente sobre el lago Paranoá. Bautizado como J. K. —rememorando al que fuera presidente de Brasil e impulsor de su capital administrativa, Juscelino Kubitschek—, esta infraestructura destaca tanto por sus características estéticas y técnicas como funcionales. El J. K., con sus 1200 metros de longitud y la totalidad de sus pilas sumergidas, supone un importante avance en las comunicaciones e la zona.
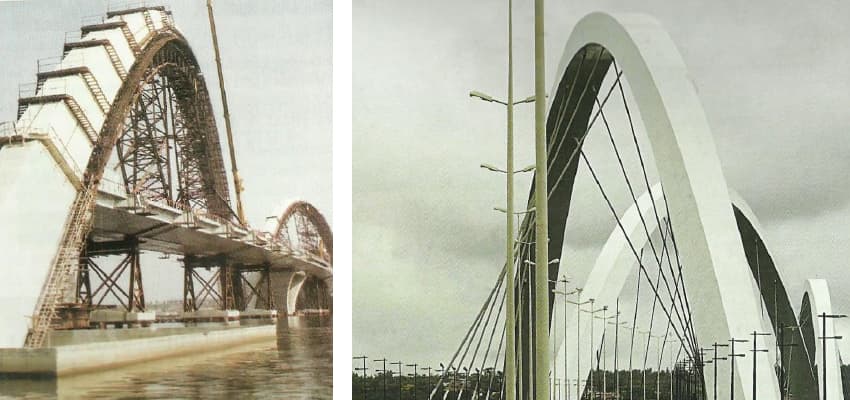
Al enlazar el sector de Clubes (plano Piloto) con el Lago Sur (QL 26), el puente Juscelino Kubitschek ha conseguido reducir el recorrido de 30 mil usuarvios diarios, en casi unos 22 km. El denominado puente J. K. ha logrado, también, que los otros dos puentes que cruzan el lago Paranoá se descongestionen de tráfico rodado, ya que a partir de la construcción de esta nueva infraestructura han quedado liberados de absorber el importante flujo de vehículos que circulaban por los mismos durante las horas punta. Este puente tiene la particularidad, sobre otras obras de semejante funcionalidad, de tener todos sus bloques de asentamiento sumergidos y unos arcos, en los que se apoyan los tableros, que cruzan el puente de manera oblicua.

Pero si este puente destaca por su importancia para las comunicaciones de la zona, también sobresale por sus características: cuenta con una extensión longitudinal de 1.200 m, dividida en cinco tramos de 250 m cada uno; tiene un radio de curvatura en planta de 3.150 m, y una rampa ascendente hacia el centro del puente del 2,5%; apoyándose, los tres centrales, en arcos que cruzan oblicuamente el tablero y los tramos de acceso a los vanos en arcos, dividiéndose cada tramo de acceso en cinco vanos con una luz que oscila entre los 45 y 48 m.
Singular belleza
Para dotar al conjunto de una singular belleza, el arquitecto Alexandre Chan proyectó todos los encepados sumergidos.
Los tableros de los dos tramos de acceso se proyectaron con estructura mixta de vigas metálicas (SAC-50) y losa de hormigón. Asimismo, los tableros de los vanos de los arcos se diseñaron con losas ortotrópicas de sección trapezoidal, con 24 m de ancho y 3 m de canto, todo en acero (SAC-50), llevando la superficie de rodadura un revestimiento de una capa de ‘Dermasfalt’, con un espesor de 8 mm.
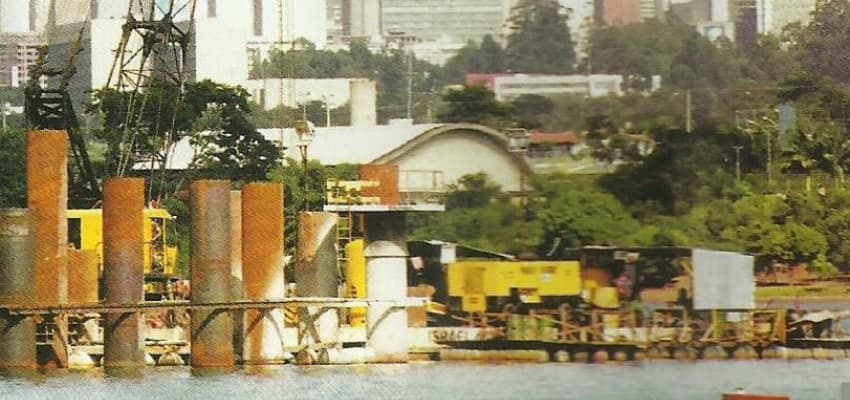
Los puntos de arranque de los arcos de sección trapezoidal variable (tramo de encepado hasta el nivel del tablero) se ejecutaron con hormigón armado y el resto con estructura metálica. La sección del arco oscila desde los 6,50 x 5,00 x 2,50 m en la base hasta una sección rectangular de 5,00 x 3,00 en la clave.
Las calzadas están separadas entre sí y de los paseos laterales por barreras de hormigón del tipo New Jersey. Lateralmente las aceras van protegidas con dispositivos de chapas metálicas y cables de acero, que incorporan en su parte superior un tubo metálico que funciona a modo de barandilla.
Este proyecto, de imponente belleza estética ha presentado sin embargo dos grandes inconvenientes en su realización: los encepados sumergidos, muy caros de ejecutar; así como los arcos que pasan a los encepados grandes cargas horizontales (3.200 t). Por otra parte, cabe destacar la elevada torsión que se impone al tablero debido a la colocación excéntrica de los tirantes.
Además de las plataformas para el montaje de los tableros ejecutados en los dos extremos del puente, del taller mecánico y construido también dos muelles de embarque, uno para las camisas metálicas y para el armado de los pilotes y otro para los tramos de los arcos metálicos.
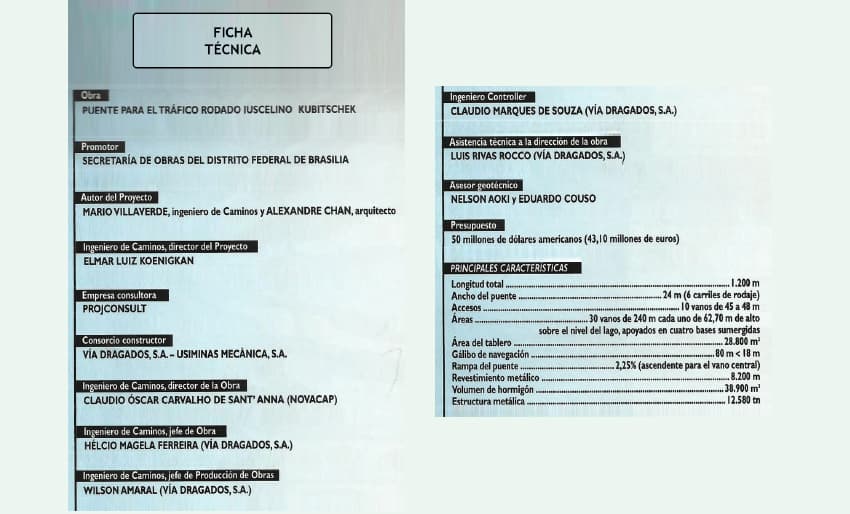
Las plataformas se construyeron conservándose el mismo radio de curvatura y la misma rampa longitudinal del puente.
Al estar ubicado en el interior del país, a más de 1.000 km de litoral, hubo que proyectar y fabricar las plataformas flotantes para los equipos de ejecución de la obra, como por ejemplo grúas, perforadoras, accesorios y muchos otros elementos.
Cimientos profundos
Cimientos con aire comprimido-Pilas de accesos y Pila 5
Al principio se hincaron las camisas metálicas con una guía suspendida y un martillo Delmag D44. La guía suspendida se apoyaba en una grúa con esteras y lanza estacionada sobre la plataforma flotante, fijándose por medio de anclas y cabestrantes. Se utilizó una Estación Total.
A continuación, se construyó una plataforma de trabajo que se apoyaba también en contrapesos de hormigón y se llevó a cabo el montaje de las campanas de aire comprimido, soldándose en los revestimientos metálicos.
Las excavaciones se ejecutaron manualmente con martillos neumáticos y sobre todo con explosivos.
Una vez acabadas las bases ensanchadas, se montó el armazón y se ejecutó el hormigonado con la ayuda de una bomba de hormigón.
La profundidad de estos tubos oscilaba entre los 15 y 22 m.
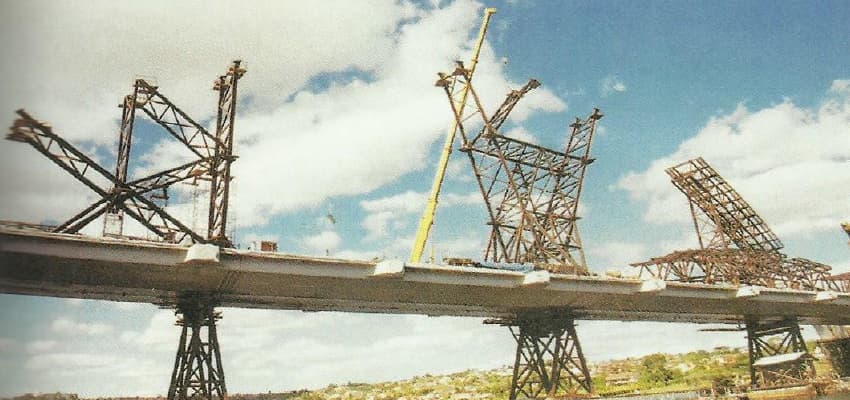
Cimientos con pilotes entubados flotantes con una capacidad de 800 toneladas
La colocación y el enclavamiento de los revestimientos metálicos se ejecutaron del mismo modo que los cimientos con aire comprimido penetrando estos en el suelo como media unos 12 m, tras alcanzar la cota de enclavamiento.
Estos pilotes se ejecutaron en dos fases. La primera, con la ejecución de tan sólo los pilotes verticales, y después de colocar el encepado en su cota definitiva, se ponían los pilotes inclinados.
Una vez realizada la hinca de las camisas metálicas, las perforadoras Wirth se acoplaban en la parte superior de los tubos metálicos y se ejecutaba la perforación de las mismas, hasta 12 m por debajo de la extremidad inferior de las camisas. Tras concluir la perforación y la limpieza, se bajaba la jamba de armadura y la trompa de hormigonado, bombeando desde una distancia de hasta 600 m.
Encepados sumergidos
Sobre los pilotes verticales se montaron las plataformas metálicas para el apoyo y la ejecución de las paredes y fondo del encepado (molde). Una vez construido el molde del encepado, se ejecutó una estructura de perfiles metálicos para el soporte de los 29 gatos de izado, con una capacidad de entre 250 y 500 t. cada uno.
Al principio, el bloque se levantó para llevar a cabo la retirada de la plataforma inferior, y a continuación se iniciaba el proceso de bajada del envoltorio que se bajó verticalmente unos siete metros hasta alcanzar su posición definitiva. Esta operación duraba una media de 12 días por encepado y para realizarla se necesitada un efectivo de 35 hombres.
Para los encepados menores, esta operación se llevó a cabo con cuatro gatos de izado con una capacidad de 250 t por gato.
Una vez fijado el molde en la cota definitiva del proyecto, se ejecutaron los pilotes inclinados a través de los agujeros practicados en la losa de fondo del molde de envoltura con la ayuda de una plantilla que fijaba las inclinaciones y la dirección de cada pilote.
Dado que la parte superior de los encepados se encuentra bajo el nivel del agua, se ejecutó un complemento provisional de las paredes para que se pudiese llevar a cabo la retirada del agua del interior del encepado.
Las siguientes fases fueron el montaje de la armadura y el hormigonado del encepado, que se realizó en capas de 70 cm de altura para controlar la temperatura del macizo de hormigón.
Teniendo en cuenta que el inicio del arco de hormigón sobresalía más allá de los límites de los encepados en más de 15 m resultó necesario ejecutar plataformas apoyadas sobre pilotes provisionales que soportases la cimbra inclinada. Los hormigonados se ejecutaron en módulos de seis metros de largo.
Transporte muy complejo
Los tableros metálicos se realizaron en Usiminas Mecânica S. A., fábrica situada en la ciudad de Ipatinga, en el estado de Minas Gerais, a una distancia de 1.000 km de la obra, y se transportaron en plataforma de 3 ejes (con una capacidad de 25 t), lo cual hizo que fuesen necesarios aproximadamente 650 viajes.
El montaje de los tableros se llevó a cabo sobre tierra en los extremos del puente y se empujaron sobre los pilares.
Los lanzamientos se ejecutaron por medio de gatos hidráulicos, reaccionando contra las pilas, proyectados para soportar también dichas reacciones durante las fases de lanzamiento (que fueron superiores a las cargas de trabajo). El enlace de los gatos hidráulicos con el tablero se realizó a través de vigas de tiro soldadas en el fondo del tablero.
Para que los tableros pudiesen vencer los vanos de 240 m hasta que se montasen los arcos y se armasen los tableros, fue necesario construir tres puntos de apoyo provisionales por cada vano, reduciendo el vano libre durante la fase de montaje a aproximadamente 60 m, que se puede salvar con la propia estructura del tablero metálico. Tras concluir el empuje, el tablero se gateaba y se retiraban losa aparatos de deslizamiento de modo que se sentasen sobre los aparatos de apoyo definitivos.
Perfecto acoplamiento
Los arcos se fabricaron en el mismo lugar donde se realizaron los tableros; a una distancia, por tanto, de mil kilómetros del lugar donde se ejecutaba la obra. Por ello, tuvieron que ser transportados a esta y, debido a su forma geométrica, totalmente variable, se tuvo que llevar a cabo un montaje en blanco en el propio taller, enlazando los módulos entre sí para garantizar un perfecto acoplamiento durante el montaje en la obra.
Los arcos se dividieron en módulos que oscilaban en longitud entre los siete y quince metros, y entre 40 y 60 toneladas, en peso; compatible, en cualquier caso, con la capacidad de carga de las grúas movilizadas para esta operación (de 250 y 300 toneladas).
Para soportar el peso de los arcos y garantizar el perfecto posicionamiento de los mismos, se montaron torres y vigas cruzadas, proyectadas y construidas al milímetro para tal objetivo.
La última unidad del arco se ejecutó siempre por la noche y con las más bajas temperaturas, ya que la incidencia del sol durante el día llevaba un aumento de la temperatura de la estructura del arco y la dilatación de la misma provocaba un levantamiento del arco, liberando las vigas de apoyo que se retiraban entonces.
Tras finalizar el montaje de los arcos, se realizó la instalación de los tirantes y se aplicaron las cargas previstas en el cálculo, siguiendo rigurosamente la secuencia establecida en el proyecto, que produjo la liberación de los puntos de apoyo provisionales retirados entonces, quedando las cargas de los tableros completamente transferidas a los arcos y pilares.
Años de control
Al tratarse de estructuras especiales, totalmente diferentes de las convencionales que existen en el mundo, las del puente J. K. están siendo comprobadas y controladas desde el principio del montaje de los arcos, y dicho seguimiento se mantendrá durante tres años. Básicamente este control consiste en células de carga instaladas en cada una de las bandas extensométricas. Están localizadas en los puntos estratégicos de los arcos, a fin de comprobar las tensiones de las chambas de la estructura, las medidas de los desplazamientos de los encepados y la prueba dinámica de la estructura con vehículo tipo, después de la inauguración y con el puente cargado con tráfico diario.

El ’Dermasfalt’
El revestimiento de las chapas de acero para la capa de rodadura se realizó con un asfalto especial de 8 mm de espesor llamado ‘Dermasfalt’, siendo sus principales características una gran adherencia a la superficie metálica y resistencia frente al desgaste.
Por último, podemos afirmar que el proyecto ha cumplido todos los objetivos propuestos: tener un puente que cumpliese la finalidad propia de una estructura viaria y que fuese al mismo tiempo un monumento más integrado con los otros existentes en la capital brasileña, cuyos autores han sido los grandes arquitectos, Óscar Niemayer y Lúcio Costa, que proyectaron Brasilia.